– Good afternoon, I’m Johanna Oosterwyk. I work at the University of Wisconsin-Madison, and I’m the instructional greenhouse manager for the College of Agriculture. I also teach classes in greenhouse cultivation for the Department of Horticulture, and I’m an Extension specialist, specializing in greenhouses, indoor plants, and general horticulture. So I’m glad to talk to you today. I’ve had a lot of questions lately about this great new fad that’s being proposed and promoted all across the U. S. and all across the world, so I’m happy to share with you about vertical agriculture. They promise a lot. Increased yields, reduced land use. Here are some typical claims made by proponents of vertical agriculture. Fresh, local produce using less resources and less land. That’s the goal and that’s the promise, and it’s one that I can sympathize with. A while back, I bought a sandwich for lunch, the same one they make copies of all across the UW campus. Bought it at a kiosk, took it back to my office to eat, and was really disappointed when I opened it up to add some mustard. That one sad-looking lettuce leaf had probably sat in a cooler for a week, been trucked across country. But, you know, we tell our kids, “You get what you get, eat it. ” And then I went, “Wait. I am a greenhouse manager. I am teaching my students how to grow lettuce.” A much more satisfying sandwich for me was a few steps away, growing just down the hall. Can everyone have that experience? Can everyone have access to that? Now, my lettuce was not grown using vertical agriculture techniques, but they can be used for that crop.
But I do wanna do a little bit of clarification and some definitions to start out with. What I teach mostly in my classes is controlled environment agriculture. Greenhouse agriculture, growing indoors. In greenhouses, these are transparent, heated structures. They may include supplemental light, but they’re usually a single layer of crops. A plant factory, on the other hand, is a structure that is insulated, perhaps a warehouse or an old factory that’s been repurposed, and no natural light is given to the crop. It is all supplemental. All electrical grow lights. So I wanna, you know, give you some definitions as I talk. So no natural light is used, it’s all electric, and crops can be in single or in multiple rows. It simply depends on the growing system. So this is controlled environment agriculture, and vertical farming, the way it’s being proposed today, is a subset of that. And a lot of the benefits of vertical farming, vertical agriculture, are already available through controlled environment agriculture. With a greenhouse, with an indoor farm, we can grow all year round instead of relying on our climate in Wisconsin, which is good about May to September. Maybe you can stretch it out a little bit with cool season crops. So with controlled environment agriculture, we can grow anytime.
We can also grow anywhere. We increase our production capacity by using otherwise unused space. Places that aren’t a field, but can be the roof of a building, can be abandoned warehouses, can be other adapted structures.
Both of these systems, in fact, all of controlled environment agriculture requires considerable resources, energy, equipment, structures, labor, often including hydroponics, which comes with special skills. But when you take growing any time and in any space, multiply those together, and you find out that greenhouses and indoor farms are bigger on the inside. They multiply the possible yields that you could have in a field on that footprint. Vertical agriculture technology adds on to this. It adds another dimension, and we think not just in area, square feet, but in volume, cubic feet, because we can layer crops on top of each other and grow up in addition to growing out. And we increase our space efficiency. We grow vertically, we grow in layers, and we’ll combine that with controlled environment agriculture and with other space-saving technologies and automation. But to do that, we need additional resources.
We can grow in layers, one plant on top of the other, but we are going to have to add light. And not just a little light. Humans and plants see light differently. Plants, potatoes excepted, do not have eyes. [audience chuckling] They don’t see light visually. They use it for energy. And for our houseplants, the light in our homes is fine. They’re pre-selected from tropical understory plants that naturally grow in low light conditions. Unfortunately, most of our food crops are high light plants. They need lots of light. You could bring your tomatoes inside from the garden, and they would like the temperatures and the moisture you give them. You could treat it like a houseplant, but it would wither because of not enough light, and it would not produce flowers. It would not produce fruit. No plant’s natural habitat is inside. How much does light matter? Here, I have some radishes growing in my greenhouse. The ones on the top, I gave supplemental light to. 350 watts per meter squared. That’s a measurement of the light energy. The ones on the bottom are covered by a shade, and they are getting 75 watts per meter squared. Much, much less. Here, they are pulled out for you to look at. The one on the left was grown in shade. These are both radishes, planted at the same time. They’re the same age, same temperature, moisture, nutrients, but without light, the radish can’t make enough carbohydrates, sugars, to make a radish. Each layer of crops in a vertical farm is going to shade the others, so without supplemental light, we are gonna have sad radishes. Outdoors, a typical sunny day, you get 440 watts per meter squared. Even in a greenhouse, that gets cut about by half by the shade from the structure, by the glazing material. In your typical office, we’re looking at two watts per meter squared of energy. We need more light if we are going to grow with plants stacked on top of each other. Here’s another example. Plants on the left, grown with grow lights. These are microgreens. Plants on the right, grown with a dark shade cover and then taken off after four days. For crop plants, light is going to be key, and without enough light, we are not going to succeed.
This has been a problem that has been a struggle for controlled environment and greenhouse growers for over 100 years, since we first started growing in greenhouses in the mid-1800s. The American Florist was a grower magazine from the time. You can’t make sunshine, so don’t try and grow tomatoes and high light crops in the middle of winter. It’s just not going to happen. But right about that time, some interesting things were happening with technology. We had the Edison light bulb. Maybe we can make sunshine. Early experimentation at Cornell University showed that yes, plants could use electrically-produced light to grow. They called it electroculture. Liberty Hyde Bailey was a professor at Cornell at the time. If you’re in horticulture, you’ve probably read some of his books or heard about him. But he proved that while it could be done, and it even improved crop production, it simply wasn’t economically feasible for food crops. It didn’t make sense. It cost more to grow the plants than you would get out of selling them. That problem has vexed growers for ages, and still today. This is a picture outside of the greenhouse that I manage on the UW campus, but there are signs like this dotted all across the campus. They celebrate notable advances by UW researchers: the Babcock butter fat test, the discovery of warfarin. In terms of advancements that are making indoor agriculture and vertical agriculture possible, I hope someday the UW Foundation will celebrate this one.
So this information I pulled from the U. S. Patent Office, and it’s important to my talk because in 1988, an application was filed for the first light-emitting diode grow light, and it was filed by researchers at UW in the Wisconsin Center for Space Automation and Robotics. Ted Tibbitts was a professor in the Department of Horticulture, and a key researcher in the area of plant grow lights. That research was funded by NASA, and they continue to have a strong collaboration with UW to this day, still working on grow lights in part because they know that they are going to need to grow plants in space if we are going to go and live long-term anywhere besides this planet. And crop production’s gonna be, like I said, a big part of that puzzle. For our purposes, this resulting technology, though, was game-changing. LEDs were not new. We had red ones and maybe a few other colors in the late ’80s. But this application, this was the first LED grow light, and we can make sunlight and, with this grow light, more efficiently than ever before. That was part of the novelty of this patent application. The electrical conversion from electrical energy to light energy was significantly more efficient.
Over the past 20 years, that technology has continued to improve. When the greenhouse I manage was dedicated in 1997, high-pressure sodium lights were the best option that we had. They’re represented by the black line on this graph. But over the years, LED light fixtures, represented by the blue line and the red line, have improved and surpassed the efficiency of high-pressure sodium lights. The blue line is for a white LED. Even more efficient are a mix of red and blue LEDs. And you can choose either one for growing crops. Now, today in 2023, LEDs are becoming the standard for indoor cultivation, especially because they are more efficient. You get more light energy out for electrical energy in. This past summer, with help from the campus Green Fund and their grant program and donors to our 25th anniversary campaign, we replaced more than 50% of our high-pressure sodium lights with LEDs. I went for the white LEDs. They are slightly less efficient than the red-blue ones that give you that fun purple glow, but I’m a teaching greenhouse manager, and being able to see the plants is very important for my students, so I chose to go for a little less of energy efficiency because of the importance of the educational experience for my students. If I were a commercial greenhouse grower or indoor farm manager, I wanna eke every photon I can out of my electrical wattage. But we are now growing more efficiently and using less light fixtures. So I started with seven HPS fixtures in each room, and I am getting by now with six LED fixtures. More light in total is getting to my plants, though. Finding energy efficient options is essential to growing indoors.
How do they compare specifically in a side-by-side comparison? Well, we have those numbers. So these data came from the City of Sacramento, comparing an indoor farm, so no natural light, all supplemental light. The picture on the left is a high-pressure sodium grow room, and the picture on the right is a LED grow room. They are growing cannabis. A 10,000-square-foot facility is going to draw about 550 kilowatts as it lights. Compare that to a typical office space, eight kilowatts for a 10,000-square-foot office building. Plants need a lot more light than we do as people. They calculated that the energy consumption for one cannabis plant was about the same as seven residential refrigerators for a year. But here are the energy results comparing LEDs to high-pressure sodium. So the left side, one round of high-pressure sodium lights. Light ends up being up to 50% of your energy use for a greenhouse or indoor farm. 41% of the high-pressure sodium was lights. That got reduced to 35% with the LED fixtures. Other electrical energy was for your plug load for motors. Maybe you’re pumping water, fan power, heating and cooling. But there’s a clear gain from growing with light-emitting diode fixtures over high-pressure sodium. We can grow entirely under supplemental light. But is that always the best option? Do we have to grow without natural light? What’s the difference?
Well, think about how you make light if you’re growing under electrical lights. The best icon I could find for an electrical light, oddly enough, was an incandescent light, which is so inefficient we would never use it for indoor grow lights, but it says “Hi, I’m a light bulb,” to everyone. But all of that electrical energy comes from power plants. And even if you’re using renewable energy, 60% of U.S. electrical grid still relies on fossil fuels. Every step in this chain loses energy efficiency. And I have a picture here of a plant feeding that fossil fuel, coal mine, or whatever. We like to joke about fossil fuels being dinosaurs. Fossil fuels are older than dinosaurs. They are results of Carboniferous swamps and plant and algal material laid down. So your coal mine is not actually mining dinosaurs. It’s older than that. But all of those plants and those algae got their light from the sun, and we lose efficiency at every step, so why not just use sunlight? It’s free.
So compare a plant factory, growing under entirely supplemental light, to a greenhouse. This was a model, not an actual case study, but computer model done by university researchers at Cornell, looking at plant factory and greenhouse cultivation. What would the potential energy use be? And they also modeled a couple of different climates. So they Minneapolis, Minnesota, where it is cold and humid. They modeled Phoenix, Arizona, where it is hot and dry. Any way you slice it, controlled environment agriculture uses energy. So these are the data for Minneapolis. The top two bars are two different plant factory scenarios. The lower bars are two greenhouse scenarios. Both use a lot of energy, but the plant factory uses three to four times as much energy for light. If the greenhouse opens its outside vents to cool in the winter, it ends up using more energy for heating. That’s what the distinction is between the two different types of greenhouses. A typical home uses 38. 6 gigajoules. This is another energy unit. But a typical home uses 38. 6, less than 40 gigajoules per year. And here, in a greenhouse, in the cheapest greenhouse scenario, it’s 60 just for ventilation and cooling. Controlled environment agriculture uses a lot of energy. There is really no way to get around that. Sometimes it’s worth it, sometimes it’s not, and we’ll talk about when it is worth it.
So the different distinctions. Well and poorly insulated, ventilating with outside air or not makes it more or less expensive to run your greenhouse or your plant factory. As real estate agents tell us, location matters, so what your local weather is like also has an effect. A plant factory maybe makes sense in Minnesota, where it gets cold in the winter, so you save money on heating. But in a sun-rich place like Arizona, what’s going to justify the cost of lighting a building when you have so much light around you, and you don’t have to heat as much? So which makes more sense, a greenhouse or an indoor farm? Might be a little easier to compare this data this way. This is looking at cost. How much does that energy cost? On the left, we have the plant factory. On the right, we have the greenhouses. And the orange bars are for Arizona, and the blue bars are for cold places like Minnesota. In either place, or in either case, the plant factory or the greenhouse, it takes less energy to run in Arizona than it does in Minneapolis. And in both cases, a plant factory uses much more energy. Again, that increase in light energy than a greenhouse does. Anything we can do to improve light efficiency, to improve energy efficiency is going to help these facilities.
LED lighting and controlled environment agriculture, I’ve already used up half our time talking about. When am I gonna talk about vertical tech and vertical farms? I have one more thing to tell you about light-emitting diodes and grow lights before I get to vertical tech. What I’ve shown you so far is mostly models and demonstrations of single-layer technology. What’s special or specific to vertical agriculture is that multi-layer cropping, and LEDs make vertical cropping possible, not just because of light efficiency, but also because of heat and how they produce heat. So here’s the data again from the Sacramento case study, where they were growing cannabis side by side in high-pressure sodium rooms and LED rooms. Again, under sole-source lighting, so no natural sunlight. The blue line is the high-pressure sodium. The two orange lines are the two different LED grow rooms that they used. But this is their total energy consumption broken down by the different energy uses. And in addition to reducing energy use for lighting, the LED rooms had reduced energy use for heating and cooling. In fact, the only place that they increased under LEDs was fan power, moving the air around within the space. This happens because of the way that LED lights produce light and the way that they produce heat. So heat production from grow lights. If you look at those two pictures, you can feel the difference in heat in those rooms. High-pressure sodium fixtures radiate infrared light. When they’re radiating visible light and light under PAR for the plants to grow, they’re also radiating infrared radiation, heat.
Light-emitting diodes radiate in very specific wavelengths. They only radiate visible and photosynthetically active radiation, the light that plants need. The heat that they produce is not produced as radiant visible light energy. It’s conductive; it actually goes out the back. It has to be removed because otherwise, the circuit that the light-emitting diode is will overheat. But it doesn’t heat the plants as they grow, and because of this, we can grow plants much closer to the light fixtures than we can with high-pressure sodium. When my plants grow on their benchtops and get up tall and reach close to the lights, if they’re high-pressure sodium lights, the leaves curl and burn because they get hot, but that doesn’t happen with an LED fixture. So with LEDs, we can grow stacks of plants, one on top of the other, mere inches rather than feet or yards above, so you can get eight to ten layers of crops in a single space. They do produce heat, but if you have the lights right below the growing point, most plants actually like to have warm roots, so it can increase your growth if you’re growing something like, say, microgreens. And that’s where LEDs benefit vertical agriculture.
We can grow short crops very, very close to each other. That means stacking is possible, and we maximize our space vertically as well as horizontally. So here’s an example of a vertical farm. It’s grown in a greenhouse using natural light as well as supplemental light, but it makes more efficient use of available space. The greenhouse using vertical ag technology fits 10 acres of growing capacity on a tenth of an acre of land. And this one’s in Wyoming. They do this by using vertical tech. This is my greenhouse, where I’m teaching students how to grow using controlled environment agriculture and to use vertical technology and vertical techniques. We’re trellising these cucumber plants. You can grow things in tiers, on stacks if you have additional supplemental lights.
Automation, like carousels that bring the plants to the workers instead of needing to leave the space for aisles and walkways also add capacity to your growing space. How much capacity? Well, in this simple cucumber system, if you grow cucumbers out of doors, you know they need a lot of space. Recommendations for cucumbers in your garden is to give each plant about eight square feet of room on its own. I have these growing in hydroponic system called slab culture, and the slab that is sitting on the floor with the roots of the cucumber plants in it is about six square feet total, about 8 inches wide by 40 inches long. So closer to six square feet. But I have eight cucumber plants growing in the space that in my garden would be allotted to one. I did the calculations. About half of a square foot per plant. Sixteen times the capacity of growing in the field. It does take additional labor and resources. I need to put in the trellises. I have to teach my students how to train the plants and prune them, but it’s absolutely increasing my output and increasing my productivity without additional resources of space.
So using that information, some groups and academics have done models. This is a study and a computer model that was done in Germany, proposing a vertical farm for the city of Berlin. So they’ve listed a bunch of different crops that they would hope to grow. And the first column there on the left is the yield projected in the vertical farm due to technology like controlled environment agriculture, so due to growing all year round and optimizing light and water and temperature. The second column is the field yield, a typical yield for each of those. In this case, a hectare or an acre of land. The final column multiplies that and gives you the factor increased by stacking, by growing multiple crops in one space. This next image will give you a little bit better idea of what they’re talking about. So they proposed a 34-story building that would grow all of these crops, and each floor would be dedicated to a different crop. Their goal was, in a building on 2. 3 acres of land, so just hectares, acres of land, so just under a hectare, was to grow enough food that from this one building, you could feed 15,000 people with their total nutritional needs, 2,000 calories a day, and they would include a fish farm in the basement to provide protein. You’ve got potatoes there for your starches. So 37 floors in total, vegetables, fish, environmental control, everything all in one space, and this was the proposal. But it takes a 30-some story building. 31 stories, plus 5 in the basement for waste management and the fish farm. These are the claims that vertical farm proponents are making. I wanna take some of those common claims and evaluate them. Proposals to use less water, less land, and down there at the bottom, less energy, food miles, and food waste. Increased yields, reduced resource use. Definitely things that we can get behind.
So let’s take that first claim. 95% less water than conventional farms. Most vertical ag uses hydroponic methods. It’s a separate question from whether or not the farm is lit or unlit, or in a greenhouse or in a plant factory. It comes down to controlled environment agriculture and what kind of growing system you use. But modeling water use for a proposed greenhouse in Arizona, just hydroponic versus conventional. Given the same field area, you can grow significantly more production with a lot less water. So, yes, we have seen in practice and in models that hydroponic systems use way less water. This happens because when you put water on a field, in your garden, you lose a lot to evaporation, you lose a lot to drainage. Some of that water just goes down and isn’t used by the plant. You lose more to transpiration, water loss from the plant, because the plant uses more water to keep itself cool, so you’re losing water in a bunch of different ways. In a recirculating hydroponic system, any water that isn’t taken up through the plant to use for transpiration and photosynthesis stays in the system and gets recirculated and recycled. It doesn’t drain down into the groundwater. It doesn’t evaporate out. And by doing that, yes, you end up with 90% to 95% less water use. So check mark. Yes, less water use than conventional farm, assuming that they are using recirculating hydroponic systems.
What about the next claim? 97% less land than conventional field production. I always like to run the numbers when I see claims like this. So here is a claim from another website. And when I mention particular farms, I’m not promoting that farm. I’m just using it as an example. So Eden Green Technology proposes they are going to improve field production by 40 times and grow 500 tons of leafy greens in a 1. 5-acre field. So I ran the numbers on these. A modest yield per acre of field-grown lettuce is about 10 tons, 10 to 15, depending on what kind of lettuce you are growing, but let’s do a modest yield of 10 tons per acre. To grow 500 tons, I would need 50 acres. What’s the difference between 1.5 acres and 50? Oddly enough, it is 97%. 1. 5 is 3% of 50, so, yes, that claim holds up. And there are other facilities, like the Berlin model that I showed you, that make even larger claims. However, given the high cost of construction and the operating costs, it does take about seven years on average before new facilities of this type turn a profit. It’s a seven-year return on your investment. There’s a lot going into these facilities. They are making sense. They can do some amazing things, but, you know, be critical about what they’re promising and investigate. Do a little bit of math. Does it really make sense?
The final claim’s down on the bottom. They’ve got three different claims lumped together, less energy use, less food miles, and less food waste. I’m gonna look at the last one first, food waste. I recently had a conversation with an executive chef who prepares food every day for 1,000 employees at a Madison corporate campus. They purchase locally for their cafeteria. They also grow their own in two shipping containers that have vertical farms in them. And he told me flat out that the local produce and the produce that they grow themselves is far better quality and lasts longer. They can hold on to their own produce for a week or more, whereas stuff that is shipped in, they need to use within just a few days, probably less than a week. So having access to locally-grown produce, definitely for him, and he’s using a lot of lettuce, reduces his food waste. So check mark for that one. Yes, we have reduced food waste with locally-grown product. Whether that’s in a vertical farm or not, it still reduces waste.
The next item is food miles. Here’s another claim from the internet. Hippo Harvest recently announced a collaboration with Amazon, and they are selling their first harvests from their greenhouse facility in California, and their claim is 80% less food miles. So they’re growing their lettuce in local greenhouses, not fields, and shipping it. And definitely, if something is grown closer, it’s not being shipped nearly as far. But why do we care about the miles that our food has traveled? It does have an impact on food waste because it takes time to get from place to place. But when we talk about food miles, we’re mostly interested in our carbon footprint. And in how much carbon dioxide goes into the atmosphere because we are shipping those plants across country and using fossil fuels to burn for that energy. But controlled environment agriculture also takes energy. Field-grown lettuce with no lighting costs is shipped from California to New York, 3,000 miles. You produce about .7 pounds of carbon dioxide per pound of lettuce, so that’s the carbon footprint of a pound of lettuce that has been shipped to us from California. A plant factory in New York, to light that lettuce, produces eight pounds of carbon dioxide per pound of lettuce, assuming that you are using fossil fuels for your energy production. Does it really matter to my carbon footprint if I am buying locally-grown CEA lettuce? Now, if I’m buying locally-grown field lettuce, I definitely may get a win there. But this is the elephant in the room, and they’re not telling us about it. In fact, on this list of claims that I got from this particular vertical farm website, it’s way down there at the bottom, mixed in with a bunch of other things. Food miles. And in the case of Hippo Harvest, I’m kinda calling them out ’cause this is this week’s news. They are already growing in California, so the food miles that they are replacing are from California. They’re not shipping their produce to New York. So that’s really the big question. Can the increased production, the improved water use, the improved land use, and the reduced food waste, can that offset the energy costs? Even with more efficient lighting in a greenhouse, energy is the question. And it’s really hard to pin these companies down on what energy they are using. I tried really hard to find Hippo Harvest’s energy use and what kind of energy they are using, but there was really nothing available. Controlled environment agriculture and vertical farms rely on energy, and because the U. S. grid is still 60% fossil fuels, they’re going to be adding carbon dioxide to the atmosphere.
Another recent news story; this one’s from last fall. Washington Post was reporting on agriculture in the Netherlands. This small country, smaller than the state of West Virginia, is actually the number two ag exporter by dollar value in the world, after the United States. This tiny country has maximized their ag production so much using high-intensity techniques, like controlled environment agriculture and vertical agriculture, that they’re number two in the world, and they’re tiny. If anybody knows how to do this, it’s the Dutch. Unfortunately, they still are struggling with energy. Growers in Holland last summer and fall chose not to plant crops in their greenhouses and vertical farms because of high energy costs. It’s hitting everybody in Europe. The loss of imports from Russia. The loss of energy from Ukraine. And they went back, many of them, to their old model of cultivating their winter vegetables in Spain and shipping them to northern and eastern Europe. Same place we were 130 years ago when Bailey said, “You can do it, but it’s not economically feasible.” So the current news is maybe not reassuring, but we have seen huge improvements in technology in even the past 30 years.
So when does vertical agriculture make sense? If you are a grower, it makes sense if you can get a premium for your market. If you can grow organically, or if you can get a premium for marketing local produce, or if you can grow pesticide-free, which is easier to do in controlled environments. In a greenhouse, you can put up screens. In a vertical farm, in an indoor plant factory, you can keep that snug and tight and not have to use chemical pest controls if you do preventive work. So if you can get a premium market value for your crop, it can make economic sense for your produce. If you can get high production value. If your plants are short, if you’re growing microgreens or lettuces and you can stack them eight to ten rows high in a single room. If they’re fast growing. This is the first year I’ve done a microgreen crop with my students. We planted them one week ago. We’re gonna harvest them next week. It’s a two-week turnaround time. That means I can do 26 crops a year. I can grow a lot of microgreens. Assuming I can find a lot of people who want to buy microgreens, I’m doing pretty good. So if they are short in height, if they are fast growing, and if they are highly perishable. If they are things that you get a premium for by providing fresh because they lose quality, like leafy greens and lettuces.
So what kind of crops do we see in controlled environment agriculture, vertical farms, and indoor growing? We see leafy greens. We see herbs, microgreens. Really high-value fruit crops like tomatoes and cucumbers, peppers, strawberries, and medicinal crops like our cannabis or herbs. Things that we’re growing for essential oils that we want to have very tight control over. So you’re going to see a fairly limited range of crops produced by commercial indoor farms and with vertical agriculture. There’s one other crop that’s not on this list, and it wasn’t part of the Berlin model, where I showed you that 30-foot high rise growing indoors, and yet it was the first example of vertical indoor agriculture. Mushrooms. For over 200 years, since the early 1800s, mushrooms have been grown indoors using vertical technology. Mushrooms are a great use of this technology. Moderate temperatures, low light. You can grow these indoors in your basement, and most of the mushrooms that we eat in the U.S. are grown indoors using vertical culture. A high-value, perishable, short crop, perfect for indoor farms. I’m really surprised they weren’t included in that Berlin model because you could grow these using the waste from other crops. So I think that was a big oversight on their part. This is the first year that I’ve grown mushrooms for my controlled environment food production class. So I think we’re forgetting something that the mushroom growers have not, even though we, well, okay, I’m a horticulturist. I probably have a bias for plants over fungi. I will just admit it. [audience chuckling]
So here again is that Berlin model. Remember, they wanted in one building to produce enough food so that everybody could have a full meal, a full day’s diet, 15,000 people fed 2,000 calories a day. However, in a city the size of Berlin, where you have 3.6 million people, you’re gonna need 243 30-story buildings to do that if you want to feed everybody all of their nutrition, carbohydrates, vegetables, protein. But what if we only wanted to do those key crops, the leafy greens, and make sure that everybody got enough vegetables? So that was proposed by a Dutch company called Plant Lab. They said that with a quarter-acre building, they could produce enough fresh produce so that 100,000 people could have half a pound of vegetables every day. Lot less buildings needed for that. But that is that sweet spot where controlled environment agriculture is going to make the most sense. Produce that loses quality if we ship it. Lettuces, leafy greens, vegetables. And if there’s one thing we don’t get enough of in our diets, it’s vegetables. CDC reports that about 1 in 10 adults gets the recommended daily dose of vegetables. Resource efficiency, where else can vertical farming and indoor ag make sense? If water is scarce, using hydroponic growing systems can make the most efficient use of a scarce resource. And we saw recently, this past year, extreme droughts in the southwest of the U.S. , where most of our vegetable production is also taking place. 95% of the lettuce in the U. S. is grown in Arizona and California. So promotion of controlled environment ag and hydroponic systems in water-scarce but sun-rich systems, growing in greenhouses with water-saving technology, and in places where solar panels can make up that electrical load with renewable energy. But maybe you don’t get the energy savings there when you consider that a plant factory, in order to light that space, one acre of a plant factory needs five to nine acres of solar panels. So you have to give up that land, or, you know, instead of using solar renewable energy for certain things, do we really want to commit it to growing produce? Just this past month, California, on the other side of the coin, experienced terrible floods. This grower is standing in his strawberry field. If you’re growing in a greenhouse or a plant factory, your plants are better protected against adverse conditions. And our weather seems to be getting worse, not better, so this is another benefit of controlled environment agriculture.
So what are the benefits? Just a sum up of vertical agriculture. Doing more with less. Controlled growing conditions, producing year-round, better water efficiency, reducing inputs costs, water and fertilizer, and maximizing our capacity by cubic volume, and reducing waste by growing closer to consumers. We can grow anytime, anywhere. It’s not just a science fiction story. We can do it, but should we? It is not the answer. It has to be part of a bigger solution. It’s just one tool to feed people, and it’s not always the best choice. Where we get the best return is using greenhouses and capturing solar energy for photosynthesis and using vertical technology for space efficiency. What will make vertical farms a good choice for our communities, for our cities? It’s going to take continuing innovation. We need more renewable energy in our energy grid, and we need more efficient systems. We need increased improvement in light and heat and energy use that goes into controlled environment agriculture. We also can look at what we get out of vertical farms, and it’s not just food. We can get jobs out of vertical farms. Much of agriculture is seasonal, but controlled environment agriculture grows year-round. We can keep people employed, and we can put those employment possibilities where the people are, in cities. We can keep the food dollars in cities. Paying employees, who then turn around and spend their money, and paying growers and owners, who hopefully spend their money in their communities. And we can provide fresh, healthy, and convenient food options. As we saw, this can reduce food waste.
And what I’m interested in, and maybe excited about, is increasing vegetable consumption. We don’t eat enough vegetables, but if vegetables are convenient and easy to eat, we eat more of them. Carrots aren’t a typical controlled environment crop, but I wanna mention them because making carrots convenient. Baby carrots became a thing, you know, around the ’90s. When carrots became more convenient, people not only ate more carrots, but the overall consumption of vegetables went up. It’s not just that people ate carrots because they were easy, it was people who weren’t eating vegetables ate carrots because baby carrots were easy and convenient to eat. They’re also fairly inexpensive, and that is a sticking point. The high energy consumption, the skill needed, the resource use means that a lot of the produce out of vertical farms is expensive. So if we’re going to increase vegetable consumption, we also need to make it affordable for folks. But I was thrilled to see outside before we came in, they had a vegetable-rich option for lunch. That really made me happy. Final item I have on here is food safety. Growing in controlled environments can also reduce the risk of foodborne illnesses that can be common in food production, particularly in the leafy greens that are commonly grown in controlled environments. So thank you for listening to me, and I’m very happy to engage and listen to any questions that you all have from what I’ve shown you today.
[audience applauding]
Search University Place Episodes
Related Stories from PBS Wisconsin's Blog

Donate to sign up. Activate and sign in to Passport. It's that easy to help PBS Wisconsin serve your community through media that educates, inspires, and entertains.
Make your membership gift today
Only for new users: Activate Passport using your code or email address
Already a member?
Look up my account
Need some help? Go to FAQ or visit PBS Passport Help
Need help accessing PBS Wisconsin anywhere?
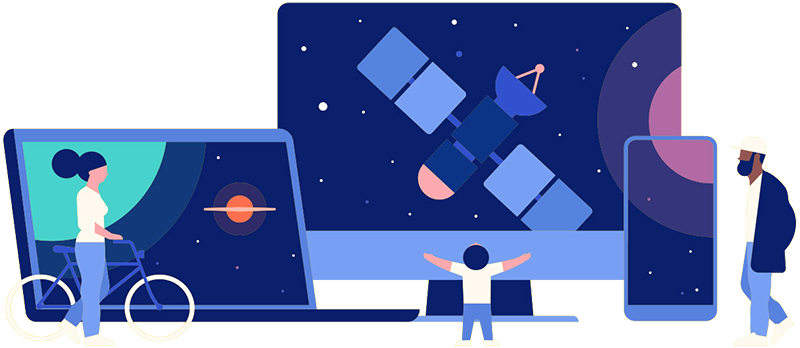
Online Access | Platform & Device Access | Cable or Satellite Access | Over-The-Air Access
Visit Access Guide
Need help accessing PBS Wisconsin anywhere?
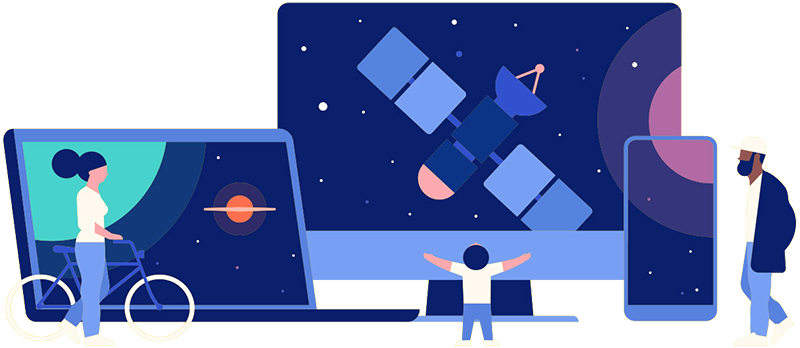
Visit Our
Live TV Access Guide
Online AccessPlatform & Device Access
Cable or Satellite Access
Over-The-Air Access
Visit Access Guide
Follow Us