Good evening and welcome to our guest speaker tonight here at Space Place. And I’m really pleased to introduce tonight Professor Matt Allen from the mechanical engineering department here on campus, and he does some fascinating work on trying to figure out how things hold together or fall apart when they’re moving at hypersonic speeds. He’s been doing this kind of work for a while. Actually was at Sandia National Labs before coming to UW-Madison a few years ago to join the faculty. And so he’s going to talk to us tonight about how to get things into space without them falling apart on us. Professor Allen.
– All right. Well, thank you. [applause] Thanks and thank you for coming tonight. I’m looking forward to talking to you. So the question that we want to talk about today is, yes, “How do desire structures or aircraft, spacecraft to get to space, “and how is that different than designing normal structures, “bridges and the things that we can do more intuitively?” So, for example, if you were tasked with designing the Statue of Liberty, say we know that we need to make this arm strong enough that it can hold up the weight of the torch there. And so we could imagine how we might, how that might put stress on Lady Liberty’s arm and where we might need to reinforce that to make sure we had enough strength to be able to hold that torch in the air. It’s not too counterintuitive. Now, what would happen, though, if instead we put a controlled explosion underneath the Statue of Liberty? And we tried to launch it into space, right? Does any of what we just talked about apply? Well, I’m hoping I can give you a little bit of an idea as to what does and what doesn’t. And it seems like a pure joke, but, actually, if you put these two structures side to side, so this is the Statue of Liberty and here is NASA’s space launch system. Now this, graphics these days are so good I have to warn you this thing has never been fully assembled. Actually, all the pieces are not even done yet. So this is just an artist’s rendition of what this may look like some day as it launches, assuming everything goes well. But, actually, if you compare these two structures, they’re fairly similar in size.
The SLS, NASA’s SLS will be a little bit taller. The Statue of Liberty is only about 450,000 pounds to five-and-a-half million for the SLS. And if you think about that, they’re both basically hollow metal structures, but the SLS is a hollow metal structure packed full of explosives that are hopefully going to propel it into space. Okay, we’ll talk about some of the issues involved in designing a structure like this. I’ll focus on the structure, not so much the propulsion or the avionics or these other things but try to give you an appreciation of what it takes to design this vehicle to survive that trip to space. A little bit more about me. What do I have, what business do I have talking about this? So I’m a professor in the mechanics program in the Engineering Physics Department at UW-Madison. I teach courses. My degrees are in mechanical engineering, and I teach engineering courses in that area.
Also courses in the astronautics/aeronautics program. And I have a research group with about 10 graduate students and a handful of undergraduates who are working on solving various problems to do with dynamics, vibration, aerospace, non-aerospace applications. Also, for the last few years, a few years ago I was invited to be a member of NASA’s Loads and Dynamics technical discipline team. This is part of NASA’s Engineering and Safety Center. So I’ll tell you about that quickly. NASA’s Engineering and Safety Center, NESC, everything at NASA has an acronym you learn quickly. They have books just to define all of these acronyms. But this was set up after the Challenger accident. And it was set up as a separate governing board, not governing board, but oversight board.
And so this is a group of experts from industry, some from academia, who provide guidance and input and oversight. So within the NESC, there are various discipline teams. You know, aero sciences, avionics, you can see the list here. And down on the list is Loads and Dynamics, the group that I’m part of. This is a picture of our team at a recent meeting. We actually got to tour the Virgin Galactic facility there. And in the middle you may recognize this young guy among all of the famous and well-known engineers around me there. Okay, but at this point I should also add a disclaimer. Anything that I say is not official statement of NASA.
I have no authority to speak for them. I just– They pay me to give them advice and that’s it. All right, so let’s dive into what we want to talk about. Before we start, we need to understand one concept. Oh, and here’s where the computer conversion messed up my equation slightly, but we’ll run with it. So first we’ll start with Newton’s second law. Dynamics. This is the core of dynamics, and it’s fairly easy for us to understand. You could imagine that if you were pushing on a car, that that force that you apply to the back of the car will eventually cause the car to accelerate in that same direction.
And the heavier the car is, the less acceleration you get. And that’s where the mass times acceleration product comes from. So that’s the basics of dynamics. The basic dynamic force is the fact that we push and something wants to resist changing speed. So this is not too big of a deal if we’re just trying to get a car to take off, but now imagine that the car is going down the road at 60 mils an hour and suddenly hits a rock, right? So now we have a huge acceleration. Now we’re on the other side of the equation. The acceleration going from 60 miles an hour to zero in maybe a fraction of a second causes a huge force on the other side of the equation. And this is one of the challenges that we deal with in dynamics. Here’s an example from the internet.
This is a Ferrari, about a million-dollar car, and the rumor has it that this car was not very many miles on it when the driver took it out to see how fast it could go, lost control of the car and hit a telephone pole at almost 200 miles an hour. And these are the pieces of the car that were left after that impact. Now, let’s back up a minute. Imagine that we took this car and we put a big rope on the front and all of us lined up and we pulled on the front of the car. How many people, hundreds of people, thousands of people, do you think it would take before we could rip off the front of the car like that? [laughter] I mean, you can’t even imagine getting enough people together to do that, right? And, yet, dynamics, Newton’s laws, did that in a fraction of a second just by getting it up to speed and hitting a telephone pole. So these are the kinds of problems we deal with. Now, if we think a Ferrari is fast, though, this picture tries to give you an idea of how fast we’re talking about when we talk about space. So a typical passenger jet here on the bottom. That goes three times as fast as a Ferrari already.
And that’s not the fastest airplane we’ve ever built. One of my favorites, the SR71 Blackbird, which would go Mach 3.3, or 3.3 times the speed of sound. So that airplane, we’re talking about 2,000 miles an hour. And we keep going up. Up here in this range are just experimental vehicles. Most of them never went very fast at that speed. And now, if we took this scale and we put another one on top of it, up into the top of the roof, and another one above that, we eventually would get to Mach 25, which is 25 times the speed of sound. That’s the speed with which the shuttle, the space shuttle, would reenter the atmosphere. And everything becomes a little bit counterintuitive at these kinds of speeds.
For example, you know that if you put your hand out the window on a hot day as you drive down the road in your car, your hand feels cooler. The air blowing by cools it off. At these speeds, the friction from the air passing over the surface of the vehicle is so great that it actually wants to melt the shuttle. And so it’s coated with these tiles. If you look closely, this is a photo I took at the museum in Washington. You can go see these now and get really close to them. And you can see every single tile has a serial number. Every little piece had to be positioned just right. And every tile would be checked after every flight to make sure that this protective layer of insulation was intact.
And some of you may have heard of the Columbia accident. Here’s an example where this didn’t go very well. So, as you may have heard, during the launch, some chunks of foam came off of the main, the core stage here, the main fuel tank, and struck the wing and did some damage to some of those thermal tiles. And, as a result, when the shuttle was coming back into the Earth’s atmosphere, some of the hot gas, the hot air generated due to the friction between the aircraft and the atmosphere was able to leak into the wing and actually melted the aluminum structure within the wing. And the wing eventually came off. And if this was Hollywood, at that point the shuttle would explode and there would be some great special effects. Actually, that’s not what happened in real life. The computers, right before everything went south, were showing that they were using their full ability to try to right the aircraft, to try to make up for this turning moment that was applied to the aircraft due to the extra drag on the one wing that still remained. But they didn’t have enough control authority to do that, and so the aircraft went into an uncontrolled tumble.
And it was at that point that the aerodynamic forces tore the aircraft apart, and these are the pieces that were eventually recovered. So this was the space shuttle hitting air, right? But hitting air at such a high speed that it generated enough force to tear the shuttle apart. And unfortunately leading to the loss of the crew and those on board. So this is why we do engineering, why we do analysis, and why we study these things to hopefully ensure that these types of accidents don’t happen again and that we design a structure that can take the loads that it will see. Here, for example, there was an adequate appreciation of the amount of force that those falling pieces of foam could exert on the shuttle. And so nobody thought, well it’s foam, it’s spongy stuff, right? What damage could that possibly do? But it did enough. Okay, so that covers the impacts. That’s just one type of load and type of problem that we might see with a launch vehicle. The other one I want to introduce is vibration.
And you can get a sense for this thinking about this child on a swing. So we all know that if we walk up to a kid on a swing and we just shake them at random, they won’t be very happy with us and they won’t really go anywhere, right? But if we time our pushes just right so that we always push whenever the child is swinging away and not when they’re coming back towards us and we time those pushes just right, they go higher and higher and higher, right? And eventually they soar into the air and everyone has a good time. That is called resonance, and that’s a fundamental property of any system. And the simplest one is this spring mass system that we could represent here. So you can imagine the child represents the mass. There’s an inertia there. The spring is a little counterintuitive here, but the gravity actually provides the spring. So hanging from that rope, gravity wants to make the child always go back to the center position. And so that’s what we treat mathematically as the spring.
And then the last property here is this dashpot that takes away some of the energy. So you know that if you stop pushing, eventually the child will come to rest, the swing will stop again. And that’s because, with very oscillation, this damping force, this dashpot, takes away some energy. So that’s a spring and a mass. And it turns out any structure can be represented as more or less a bunch of springs and masses. And so we can understand anything. Before we go there, though, I wanted to make an analogy with music. Music is also a representation of vibration. It’s a manifestation of that.
And we measure vibration in terms of frequency or how many oscillations we see in a second. So a typical vibration in music might be in the hundreds of hertz range. For example, if we took this piano and we go to the middle of the scale and we find middle C and we hit that key… [piano note] We’d hear a sound kind of like that. [piano note] And that sound that you hear is oscillations of sound of air molecules at 262 cycles per second. And also there are harmonics and other things. But that is just a vibration of the air and a vibration of a string within the piano that’s tuned to 262 hertz, transmits sound into the air, and that eventually makes it into your ears. And so musical instruments have many different keys that they’re able to play, or many different notes. Every one of the keys hits a different string that’s tuned to vibrate at a different frequency.
And by controlling that you can make great music. The same is true– [piano note] Oops. The same is true for any structure. For example, this is a bridge that I worked on as part of my doctoral research. And this bridge was instrumented with vibration sensors all along the length and on the piers. And measurements were then taken, a large chunk of concrete was dropped onto the bridge, and then the vibration that that caused was measured. And you can see a visualization of that here. So the concrete was dropped right in the center of the bridge, and you’ll see this restart in a minute. And you can see that initial impact.
Yep, there it is. And you can also see how that turns into a vibration of the bridge. Now, the real bridge didn’t bend this much. I’ve amplified that in the simulation. The real bridge would break long before moving that much. The vibration was probably on the order of millimeters or maybe into an inch or so. But even that can be enough for a stiff structure like a bridge to cause damage and to cause an unsafe condition. But anyway, the interesting thing here is you can see the musical notes that this bridge is playing. So this looks like a complicated mix of all kinds of notes happening at once, but that can actually be decomposed into a bunch of simpler patterns, simpler deformation patterns.
And each of these has a note or a frequency that it will resonate at and that it will oscillate at when it’s struck. And so the bridge is nothing more than a piano with its notes tuned to certain frequencies. And, as engineers, we designed the bridge to play the notes that we want it to play so that it will survive the loadings that it will see as cars drive over it or as other things happen. So the same is true for a rocket. Now, this is actually a highly simplified model of the space launch system. The actual models, I’ve seen them but they’re proprietary and I wouldn’t be able to show them to you. But so, actually, I had one of my grad students just make a very simple shell structure that looks kind of like the SLS so that we could see what the vibration might look like. And qualitatively these will give you a good idea of what might happen during launch. So these are some of the different frequencies then that the vehicle might exhibit.
And you can see the different ways that it deforms. So in these two here, we see bending of the rocket. As it’s trying to ascend, the whole vehicle is bending. And those are definitely problematic because the guidance system is trying to steer the rocket and make small adjustments to the engines at the bottom to keep a steady course. And so as it detects this bending motion, it can send the aircraft off course and lead to instabilities that can cause it to crash. And so it’s critical to understand these types of motions. The other thing is that every type of motion like this puts stress on the structure in a different place. And if you can see in the video, there’s coloring to show you the hot spots where the stress is the greatest. You can maybe see that best over here.
And so engineers can decompose a structure like this into these fundamental motions and look at where the stresses happen. And if the stresses are too high, we can redesign it to try to move the stress around and eventually come up with a design that can survive that launch environment. So the other thing I wanted to point out here is that NASA’s currently under a mandate to reuse as much as possible, you know, things from other programs. So the main engines on the SLS under the core stage here in the middle are engines from the space shuttle. And so you might think that this is pretty easy. Those engines have already flown to space, we’ll just slap them on a new vehicle and away we go. But hopefully this kind of illustrates for you that as we redesign the vehicle, we changed the way it moves. And so those engines, which on the space shuttle had a certain level of vibration and certain type of motion, have a totally different one on this vehicle. And so a lot of engineering has to go in to making sure that the engines themselves can survive this environment.
They were able to survive the space shuttle vibration environment but they may not survive this one. And the same is true for every little piece. Every flight computer, every nut and bolt has to be positioned and designed such that it can take the forces that it will see. So let’s go through in a little more detail and talk about the different stages of launch and the different loadings that we see. And I’ll use the space shuttle as an example because we have some open public domain information on this. So this is a picture of the space shuttle on the launchpad. And the shuttle was tied to the launchpad through four posts under each one of the solid rocket boosters. I think these were on the order of one-inch steel or something like that. And those posts would hold it there, and the main engines on the shuttle would be fired up.
And you can imagine that would cause the whole vehicle to want to kind of lean over. It will also take some of the weight. Originally those eight posts are holding all the weight of that vehicle. Well, that takes some of the weight off and it causes the vehicle to kind of flex over. But it doesn’t stay there. It, just like the kid on the swing, it swings a little farther than it wants to and starts to come back. And they call that the twang. The astronauts who were right at the top, they’re seated up at the very top of the shuttle, would feel this swinging motion, this twang, that happened at about one cycle per second or so, similar to the kid on the swing. And a little after that twang was over, some explosive bolts at the bottom of those posts would release the shuttle, and it would begin to ascend.
And so we’d see the solid rocket boosters going and the main engines going. And you can see the fire coming out of the solid rocket boosters. They’re a solid propellant. The main engine burns hydrogen and oxygen, which makes an invisible gas. But anyway, all of that thrust would drive the vehicle to higher and higher speeds. And as the vehicle is ascending, the air is getting thinner and thinner but its speed is getting higher and higher. And higher speed means more force from the wind, more air, more drag. But the higher altitude means less air, less drag. And so if you compare those two forces, the space shuttle eventually reaches a point called max Q, or maximum aerodynamic pressure.
And that’s one of the critical places during the launch profile. The vehicle is under tremendous pressure from the front. This picture, this is actually a picture of a shockwave on the vehicle. But it gives you an idea of the pressure that it’s feeling. And so for the shuttle this would happen about one minute into flight, and it would– So the vehicle would hit this critical speed, and to make sure that the vehicle survived, we’d do two things. We’d throttle back the main engines to slow the acceleration a little bit to reduce the load, and the solid rocket boosters themselves were actually designed so that at this point of the flight the thrust would scale back to 71% or so of the nominal maximum thrust. So all of that would happen and we’d get through this point of maximum shaking, maximum noise, and the vehicle would eventually break free of the air and get to even higher speeds. – What speed is it at when it hits max Q? – You know what? I don’t know off the top of my head. Yeah, good question.
I know the information I found said it’s one minute into flight, about 35,000 feet. The other piece of data I can give you is within a few minutes of launch– we launch in Florida– within a few minutes of launch it’s over Europe. So you can do the math and figure out how many thousands of miles that is in a couple of minutes, right? But, yeah, good question. Okay, so shows you the full profile. And I’ll show this just to mention one or two other events. Once we get into space, there’s no more air, things get much easier to deal with. The last main event that we have to worry about is the separation of the boosters and the main tank from the vehicle. And this picture shows a test that’s done on the noise of a rocket. Here’s an explosive going off to simulate this stage separation event.
And, you know, we can’t just cut a string and let them go. These, they’re subjected to huge forces, so there’s strong connections holding them there. And so it takes a powerful explosive event or something to break those boosters free. But we need to be sure that the shockwaves that that explosion sends into the rest of the vehicle doesn’t damage it. And so a lot of testing goes in to make sure the electronics and the vehicle can survive those events. And you can also imagine how the current SLS is going to be more of a challenge in the shuttle. The shuttle is kind of riding here, kind of loosely connected to this main tank. And these two boosters are connected to the main tank as well. So those blast events will put a lot of loading onto that main fuel tank, but we’re going to drop that in a while so it’s not as critical as putting it on the launch vehicle itself.
Okay, so that’s the launch and the flight environment. To put some numbers on some of these things, I’ve taken some numbers from the Delta IV rocket’s launch handbook. So this is a handbook that’s out there. If you were designing a payload to go up on the Delta IV, this gives you all the information that you would have to design your satellite or your payload so that it could make it safely to space. So the first thing that you would think about is static acceleration. Because the rocket is accelerating at such a rate, it’s accelerating at a rate of six times or five times that of gravity, so the total acceleration that you would feel in the rocket could be 6 Gs or six times out of gravity. So if we go back to our Statue of Liberty example, we’d have to design Lady Liberty’s arm to be strong enough to hold six times the weight of that torch if we want it to get to space. So that’s what’s in consideration as we design the SLS. There’s an acoustic environment, which is measured in decibels.
So to give you an idea of what that would be like, normal conversation here in this room we have a level of maybe 60 decibels. If I fired up a lawnmower in here, we’d get up to 90. Every 20 decibels is 10 times more pressure at sound. And then a rock concert is 1,000 times louder than what we have in this room right here at 120 dB. And you go a little beyond that and you find finally get to the level that’s within the inside of the Delta IV rocket. Okay, so there’s the acoustic environment we worry about, and then last is the dynamic acceleration or all of the shaking, all of these resonant forces that we talked about. Those also can be measured in Gs, acceleration due to gravity, and this might be on the order of eight Gs root mean square, RMS. So if we had an oscillation, for example, here in blue, the RMS is a measure of the height or the amplitude of that oscillation. So we might have plus or minus 14 times gravity the dynamic motion that the vehicle is going through.
So to put that into perspective, a typical hard disk drive within your computer, if you still have one of these older spinning disk models, is designed to operate at 0.4 Gs RMS or 20 times less. And it could survive up to three Gs. So even if you were to turn it off and stow it away, at eight Gs, the hard drive wouldn’t be operational when it got to space. And so you can’t just go, you know, slap an iPhone or a MacBook on the SLS as the guidance computer. Every little bit of electronics has to be designed to be able to survive these kinds of loads. Not to mention the thermal and the radiation effects in space. Okay, so how do we do that? Well, this is actually a picture of an electrodynamic shaker about the size of me, that’s housed at UW-Madison. What it is is it’s a huge speaker, a big electromagnet here. And there’s a plate on top.
And on that plate we can mount things like this hard drive. And then we can command that plate to go through an eight G environment. And, actually, what’s done is a recording of a launch environment is actually played back, and our electronics ride out that environment, sometimes with some safety factor. And then, if the electronics survive, they’re certified to fly and they’re allowed to go up into space. So I have a little video that I can show you to try to give you an idea of what we might see here. So this is a video of a little wing structure on top of the shaker. And you can’t really see the motion of this plate. This is moving with something on the order of, you know, a launch-type environment. And as it does, you can see the huge vibration that’s being generated due to resonance of the wing.
We’re driving it right at a resonance mode. And you wouldn’t be able to see that motion either because it’s happening very quickly, but there’s a strobe light that happens to be timed with the vibration. And that’s what allows you to see what seems to be a slow motion of the wing there. So that gives you an idea, and if I had the audio file, I could play another video that would actually show you what it sounds like to be in the room. But it’s actually a very loud, unpleasant sound. [laughter] So we’ll skip over that and go back to the presentation here. Okay, so that’s our wing demo. And, actually, the first time I saw this, our technician was running it and I saw the level of vibration and I said, “That doesn’t really look safe. “Are you sure that thing isn’t going to break?” And he said, “Oh, no. I’ve done this demo, you know, for years. It’s fine.”
He’d done the demo for a minute or two once per year for years. So, you know, we thought it wasn’t a big deal. But sure enough, on this rendition, a few minutes into it, we started to hear some funny noises coming from the machine. We took it apart and this is the piece of the wing right in the back there, under the clamp. And you might not be able to see on the video but it’s actually developed a crack, and half of the wing just about cracked off, was ready to crack off. So these are the things we’re trying to design against, trying to make this structure strong enough, stiff enough, so that this doesn’t happen. And that is easy if we’re building something small. So this picture on the far left shows you a cube sat. This is a little tiny satellite about this size.
And these are relatively easy to design. They’re quite small and rigid and so it’s easy to make them such that they can make it to space without breaking. So you can actually design one of these, and for relatively inexpensive they can be added on to other payloads and put into space. Now, if we want to make something larger, like the Hubble Telescope there, it’s much larger, much more flexible, and it takes a lot of weight to stiffen the structure enough that it can survive that environment. And even more so, you know, as we make the largest and most complicated vehicle ever to be built, the flexibility is larger, the size is larger, and so it’s even more of a challenge to get this to survive the trip to space. So how do we do that? How do we make sure that our rocket can make it safely to space? Well, what we do is create simulation models. These are called finite element models because we take the part, here’s an example of a two-cylinder engine, and we break the part into lots of little squares. And for every little square we can solve the mathematical equations for force and deformation. And so the computer can help us to go through millions of squares and add all that up and figure out where the highest stresses are, where the biggest loads are.
So this method works great. The challenge is that, you know, you see to represent this complicated geometry just of this little two-cylinder engine, I already have something like a million squares, right? And our computers can’t handle much more than, you know, tens of millions of squares. Even a supercomputer might cap out at a hundred million squares. So even for a little engine like this, engineers will spend a lot of time simplifying it down, trying to figure out what are the key elements, and then meshing that with larger squares that will be, that can be run on our modern computers. Okay, so all of that work is done, that modeling is done, and we’ve made all kinds of simplifications and assumptions to make the model tractable on our computer. And so the next thing we need to do is do a test to see if that model is correct. And if the model is correct, we go forward. If not, we go back and we fix things. And in the aerospace industry an expert told me recently in 30 years of launch vehicles, they’ve had only one case where the model was ever correct the first time.
Every other case it required some updating and fixing after the testing. Okay, so those tests are done on the ground on pieces of the vehicle. And then that model is used to estimate the forces and the loading as the vehicle goes into space. And there might be thousands of load cases for each stage of flight. You know, the initial launch, 10 feet up when the weight of the rocket is reduced due to all of the propellant that’s burned already, and at every stage in flight, and especially the critical ones like max Q. And so all of those cases will be analyzed and will have key components, we’re looking at stress, and we’ll go back to the drawing board and redesign places where the stress is too high and run the simulation again and keep doing that until we have a vehicle we think can survive launch to space. So that work is underway right now for the SLS. So this shows you some of the different components. These are at various stages of completion.
The boosters are actually space shuttle boosters with one additional segment. So those are probably farthest along. And then there are various stages of completion. And so right now, as each piece is built, the actual hardware that will one day fly is being tested by applying forces, by measuring vibration. And that’s being checked against computer models to see if those models are accurate and to fix them and update them. And all of this is being done hopefully on schedule to get this vehicle ready to launch within a year or two. Okay, so, you know, I showed you earlier a computer model that my student made in an hour. Modeling a real vehicle like this is a much more complicated process. Every nut and bolt, every place you might have a failure has to be checked.
And the models are incredibly complicated. One of the most challenging things actually is modeling the places where the different components come together. I don’t have any examples of the SLS that I can show you, but I do have some pictures from an F16 fighter engine. So this is the engine of an F16, and you can see the housing here that holds it all together. And this picture shows you what the bolts look like that are holding together the different piece of the housing. And you look at that and think, well, that should be pretty easy to make a computer model of. I’ll just glue everything together everywhere it comes together and not worry about it. But it turns out that these joints are one of our biggest challenges in modeling vehicles like this or like the SLS, because those bolts don’t actually just squeeze things together. On a microscopic level, when we tighten a bolt, we actually squeeze the material under the bolt but it opens up in other places.
And there’s a complicated pattern of loading and deformation. And even more challenging is the fact that this model is assuming that everything is flat and smooth, but, in reality, there’s some roughness to the material. And so there might be a microscopic piece of material and asperity. And, you know, if we really wanted to model it on detail, we have to think about the individual atoms that are coming into contact and the bonding forces between them. That’s where friction and other forces come from. So our computers today can barely, actually can barely model this for one or two joints, much less for an entire engine. And so we have to use all kinds of assumptions. And certainly, everything down here just has to be, we have to do a test and characterize a material. None of that can be modeled currently.
So a vehicle like this, each component has to be modeled. We have simplifications, and everywhere there’s a joint we make some kind of assumption. Like assuming that we can connect all of the pieces here to all of the pieces here through one little element that will represent our bolt. And then, as the test data comes in, we can figure out what the stiffness and strength of that element should be to match what we saw in tests. So I won’t go into this here in the interest of time, but the other thing that’s important in all of this is the fact that the friction at these bolts is what gives us most of our damping. Most of the energy that’s absorbed is absorbed in friction due to these joints. And that’s something that we can’t predict. That has to do with these microscale and nanoscale effects. So we rely on testing today just as we did, you know, even in the 1960s.
And why do we care so much about this dissipation? Well, just as the child on the swing, if we apply a force, the vibration amplitude grows. And the only thing that can limit the amplitude of vibration is the damping or the friction and dissipation within the structure. And if we get the damping wrong, suppose our computer model tells us that this red curve is the damping level that we have, when in fact, we have less damping, we have the blue curve. Well that’s twice as much vibration, twice as much stress, twice as much loading. And on launch day that could have disastrous effects because if we haven’t designed for that, components can fail and our vehicle goes up in flames. Okay, so hopefully I’ve given you some appreciation for why this still is hard. It’s hard to imagine that, you know, in the ’60s we designed a space shuttle using computers like the ones you see there. Now we have Google data centers with– You know, I don’t even know what the number is. It’s probably way more than billions of times the computational capacity of the computers back there.
And yet our models are still probably billions and billions of times too coarse to even begin to capture all of the physics that we might need. So we still rely on testing and updating to make sure that our computational models are correct. This same process is used for all kinds of things, for cars, you know, motorcycles, musical instruments and speakers, even cellphones to make sure that they don’t break when they’re dropped. The one difference is in all of these cases they can build a prototype, they can drive it, and they can see whether they got what they wanted and whether this structure is okay. With the SLS, the first time we will know whether we were successful is when it flies for the first time. And so that’s why so much work is going into testing each component and checking each step along the way because we’re going to put a lot of confidence in that model and we’re going to believe it when the model says, yes, the vehicle is ready to fly. All right, so I thank you for listening today. I hope you’ve got a little bit of an appreciation for some of the aspects of launch and the dynamic environments that spacecraft and other vehicles experience. And we’re excited to see what happens with this vehicle.
The testing is well underway. The first launch is expected in early 2019 at this point. And so if all of the different pieces can come together in time and all of those computer models can be tuned and everything comes together and we come up with a design that can survive the trip to space, we hope to see that launch in about a year or two. All right, and with that I’ll also just quickly acknowledge all of my graduate or some of my graduate and undergraduate students and the funding agencies that have made our work possible and allowed us to study these types of problems. And, with that, I’d be happy to take any questions that you may have. Thanks for listening. [applause]
Search University Place Episodes
Related Stories from PBS Wisconsin's Blog

Donate to sign up. Activate and sign in to Passport. It's that easy to help PBS Wisconsin serve your community through media that educates, inspires, and entertains.
Make your membership gift today
Only for new users: Activate Passport using your code or email address
Already a member?
Look up my account
Need some help? Go to FAQ or visit PBS Passport Help
Need help accessing PBS Wisconsin anywhere?
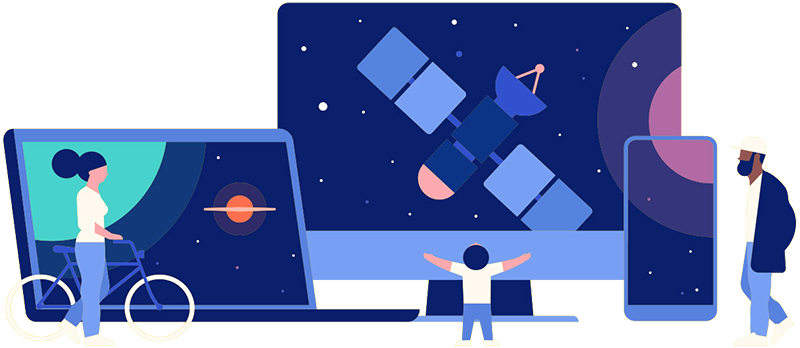
Online Access | Platform & Device Access | Cable or Satellite Access | Over-The-Air Access
Visit Access Guide
Need help accessing PBS Wisconsin anywhere?
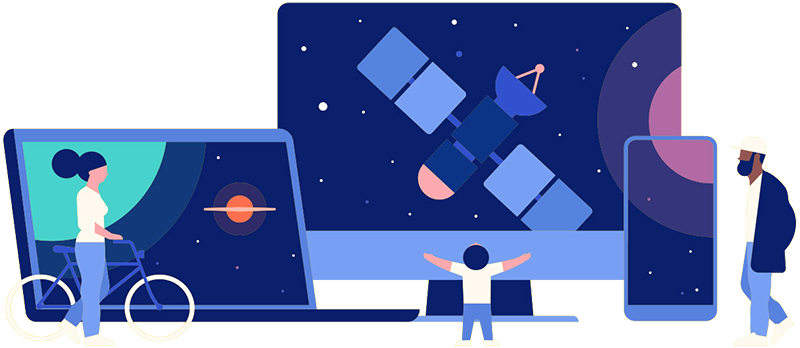
Visit Our
Live TV Access Guide
Online AccessPlatform & Device Access
Cable or Satellite Access
Over-The-Air Access
Visit Access Guide
Follow Us