– Welcome everyone to Wednesday Nite @ the Lab. I’m Tom Zinnen. I work at the University of Wisconsin-Madison Biotechnology Center. I also work for the Division of Extension Wisconsin 4-H. And on behalf of those folks and our other co-organizers, PBS Wisconsin, the Wisconsin Alumni Association, and the UW-Madison Science Alliance, thanks again for coming to Wednesday Nite @ the Lab. We do this every Wednesday night, 50 times a year. Tonight, it’s my pleasure to introduce to you Marianne Fairbanks. She’s a professor in the School of Human Ecology, and she was born in Holland, Michigan, and went to high school there. Then she went to the University of Michigan to study art and fiber. She got her MFA from the School of the Art Institute in Chicago, and she came to UW-Madison in 2013.
Tonight, she’s gonna speak with us about her invention called Hello! Loom. It’s a small, handheld loom. It’s a great introduction to the art and techniques and fun of weaving. Would you please join me in welcoming Marianne Fairbanks to Wednesday Nite @ the Lab?
– Hello, Tom; thank you so much for that great introduction. I’m here today to talk to you about Hello! Loom, an invention that I came up with back in 2016, that enables people to weave with these small, laser-cut looms. And when you’re done weaving, it looks something like this. So, before I tell you about how I came up with this invention, I would like to go into some of my own personal history that led me to weaving. As an undergrad at the University of Michigan, I took my first fibers class with Professor Sherri Smith. She was a transformer in the field by making large-scale sculptural work and enlarging a waffle weave structure. This work created a dialogue between soft loom woven textiles and large sculpture forms.
And it helped put fibers on the map as a fine art form. She was a pretty hardcore teacher, and I was reminded of this again most recently when I stumbled upon my syllabus from over 20 years ago, where she wrote, and I quote, “All of these areas are to be approached “as a way of making art forms. “It is not a home economics course “and not a course for making useful little goodies. “Garments and other usable objects are suitable only if they are of original design and very high quality. ” And this part’s in all caps, “REMEMBER, THIS IS NEITHER THE TIME NOR THE PLACE TO MAKE YOUR CHRISTMAS PRESENTS. ” So, here I’m quoting from my professor, just as an illustration of how I came to weaving as more of a art practice than a utilitarian practice. So, I was encouraged to not make useful little goodies, but instead use my art form to communicate my ideas. So, I went on to get my graduate degree from the School of the Art Institute in Chicago in fibers and material studies. I was still interested in materials and textile processes, but I also became very interested in collaboration and social practice. In my collaboration, I became interested in cultivating interactive and participatory experiences, more than making commodifiable art with a value.
So, we searched for ways to initiate and show work in new contexts and environments, places where the work might not necessarily be seen as art with a capital A, but where the audience for the work far exceeds the number of people who might see a piece hanging in a gallery. As Suzanne Lacey writes in her book Mapping the New Terrain, these expansive venues not only allow for a broader reach, but ultimately a more integrated role for the artist in society. So, that foundational idea, mapped by Suzanne Lacy, became really important to my own practice and feeds into a project that I’m gonna be telling you about, that is called Weaving Lab, that led to the invention of the Hello! Loom. So, in my collaborative group, one of the other things that we developed was a project called personal power, where we embedded small solar panels into wearable garments to charge portable electronics. The idea was to get one step closer to living off the grid. To collect the Sun’s energy, we used flexible, thin solar panels, or photovoltaic panels, and what you’re seeing here are some early prototypes of our idea. I wanted to introduce you to this project because it led to my first small business. In 2005, we translated the prototypes into a line of bags and founded a business called Noon Solar. Our prototypes got a lot of positive attention, and people seemed eager to use the technology that we had integrated into wearables for their own daily lives. So, we knew we needed to make it a product line to fulfill our concepts.
I was led into entrepreneurship through this wearable technology idea. As an artist, I was used to making one of a kind objects, but here, I became a designer and an entrepreneur. I ran the business for seven years, but ultimately had to close shop in 2010. We were pretty ahead of the curve, I think, with this project, integrating solar into wearable, but I realize how ahead of the curve we were when I think back to all the different kinds of cell phones we were trying to charge, and the fact that just three years before we closed shop, the iPhone came out. And so that was a revolutionary technology within portable electronics, as you all know. Currently, I’m an artist and designer with a creative studio practice. Most of the work I make is for exhibition. I’m interested in technology and textures around weaving. I’m interested in exploiting the scale and the language of weaving, and how the interlacements can be used to create images. I am also interested in how the traditional patterns of weaving can be used in new and innovative ways.
So now you know a little bit about why I love weaving and what I do with textiles, but I wanted to share some larger thoughts about why textiles are important. So, in this book titled Textiles: The Whole Story: Uses, Meanings, Significance, by Beverly Gordon, I learned a few succinct ideas about the importance of textiles in our culture. Textiles are a central part of human consciousness. Cloth is universally significant in every ritual that is part of our mortal journey. So many examples from the moment we are born until the moment we die, and here are seen in a baby blanket and coffin cover. So, just thinking about cloth as a protector. References to cloth and thread in archetypal and mythic stories are all over the place. So, there’s a role of the textile and weaving specifically in the Odyssey, where Penelope is married to the main character, Odysseus. When Odysseus is away at war, she is forced to remarry, and she doesn’t want to, so she devises a trick to delay the suitors, one of which is to pretend that she is weaving a burial shroud for Odysseus’ father, and claiming that she will choose a suitor only when she has finished. Every night for three years, she undoes part of the shroud and weaves it again the following day.
For three years, this went unnoticed, no one the wiser. So, a great illustration of how everyone knows weaving takes a long time, and no one really knows how long. [chuckles] And this myth is a great example of that. So, I also love the examples found in metaphors throughout our culture to communicate cultural values. Here is the DNA, our very genetic code, and the life building blocks are represented as strands that twist or ply around one another. Another classic metaphor around textiles is how when people get married, they call it tying the knot, and some even do it ceremonially in their celebrations. In her book Women’s Work: The First 20,000 Years, author Elizabeth Wayland Barber states that during the Upper Paleolithic, string was, quote, “The unseen weapon that allowed the human race “to conquer the earth. “The invention of fish lines, tethers, nets, “and leashes represent a string revolution “that was every bit as pivotal for humankind “as the harnessing of steam in the Industrial Revolution,” unquote. In the 21st century, the challenge is no longer to conquer the earth, but to sustain it, and the revolutionary power of textile technology has not diminished. From architecture to agriculture, medicine to manufacturing, nearly every aspect of our lives is touched by advances in technical textiles.
Though we rarely recognize the humble string for its contributions, it has been and remains a catalyst for countless innovations and efficiencies. As a side note, I just wanted to point out that I think one reason that textiles aren’t known for their innovations and their technological advancements is that largely, for thousands of years, textiles have been biodegradable. So they’ve been lost to the test of time as they biodegrade in the earth. So there’s not a ton of evidence of prior textile technologies that exist today. But now I wanna transition from why I think textiles are important to how they’re made and what they are. So, specifically, I’m gonna talk to you about weaving, and then some loom technology. So, here is a diagram of how weaving works. Weaving is a process of interlacing threads at a 90-degree angle. In one direction, we have the warp threads that are held in tension, normally on a loom. And the way I remember the warp threads is by thinking of, this is a side note again, but like I think of the intro for Star Wars and how the text is coming at you in your face through warp speed and warp time.
And so I always think of the warp threads coming, sort of coming in your face. And the weft threads are the ones passing back and forth through, under, and over the warp threads. So, the way to remember what a weft thread is, is to think left to right. So, while I think warp threads, Star Wars coming at your face, I think weft threads, left to right. So, that’s my secret for figuring out warp from weft. So, now let’s discuss what is a loom. A loom, the basic purpose of any loom is to hold the warp threads in tension to facilitate the interlacement of weft threads. So, here we have a frame loom. Here, we have an example of a tapestry loom, a vertical arrangement where the threads are held in tension up and down so that the weaver can hold a maquette or drawing sort of behind the loom that serves as the plan for what she’ll weave. These are warp-weighted looms, even older, which is a really cool technology where stones or sometimes ceramic objects were used to weight the warp threads so that the weaver could interlace the weft threads within that vertical arrangement.
Another favorite is the tablet loom. I love all weaving technology, as you can see, but this one is particularly interesting, ’cause it’s so simple. Originally, these were made out of bone and wood and all sorts of things. Now we can make them out of playing cards or any number of materials, but this slide is showing you some early evidence of the tablets themselves. They were excavated in Denmark in the early first century BCE. It could be even older, but again, we don’t have a lot of evidence of this technology. So, the cool thing about this technology is that, as you turn the playing card or turn the tablet, a new shed opens and you’re weaving through that opening space. So, again, tons of invention around weaving. Here is a image of a floor loom. So, as you can see, as time went on, there became more advanced ways for the loom to hold the threads in tension.
And the weaver is controlling the lifting of and the lowering of the threads with her foot. And behind me, you can see a floor loom, and this room I’m in has about 20 or 25 floor looms. So, that’s what we use to weave here at UW-Madison. Here, the next slide shows a backstrap loom. So, in many Central and South American countries, the backstrap loom is the primary loom. And one of the things that’s pretty cool about this technology is the weight of the weaver’s body is what’s holding the threads in tension, and a sophisticated system of string pedals lift the threads in different pattern variations. Here is a something called a rigid heddle loom, and of course the really cool part of this technology is that you’ll see little holes where threads either go through the hole or through the slit. And with that simple introduction of that binary, either it’s lifting in the hole or it’s sliding through the slit, you get an open shed, which is what you weave through on the rigid heddle loom. And finally, here we are at the Hello! Loom that I designed first in 2016. So, the Hello! Loom fits into the category of a frame loom, and it’s laser cut, and something that sets this loom apart, potentially, is the inset of the tools.
So, the design efficiency was really important to me when designing this loom. So it has two needles, a comb, and a stand. So you’ll see how those all come together in a few minutes. I wanted to dive in and talk a little bit more about the utilitarian and artistic potentials of weaving. So, for those of you who don’t know, and this was me back when I first got my job here at UW-Madison, there’s a relationship between human ecology, which is the school I teach in now, the School of Human Ecology, and the School of Home Economics. So, home economics, according to Merriam-Webster, was the study or class that teaches skills, such as cooking and sewing, which are useful in the home. Human ecology, on the other hand, is a brand of sociology, dealing especially with the spatial and temporal interrelationships between humans and their economic, social, and political organization. So, I bring this up because, as I mentioned before, I’m trained as a weaver as an art form within the school of art, in the place where I studied weaving. Here, we teach textiles within the design practice, and so the legacy or history of human ecology and therefore home economics has to do with a much more utilitarian past. When I first got to this weaving room where I sit now, I came across journals like this.
It’s called Practical Weaving Suggestions, and it teaches readers how to design things for their home. Here, this one is offering you the directions or recipe to make place mats that stay placed. So, as I flipped through these journals, I just became more and more fascinated with sort of how weaving patterns were disseminated to home weavers and the production of cloth for all your home needs, from clothing to curtains to bed linens. Here are a few more cover examples. I found the covers to be very enticing. And as I settled into my new job, I pored over these journals and I learned a lot about sort of the history of utilitarian weaving, how particularly women were learning weaving in home economics back or in early 1900s, when this school was founded. I continued my research by looking into weaving education around production and craft. I learned about how in early 1883, William Goodell Frost, president of Berea College in Madison County, Kentucky, created a program called Fireside Industries. This initiative was inspired by the Arts and Crafts movement and sought to encourage hand weaving and to create a fashionable marketplace for crafted goods. The program provided women with a place to sell the goods woven on their looms and inspired many other craft programs, and served as a model for other weaving cooperatives in the Appalachian Mountains.
Floor looms were used for years in cottage production of cloth, but after the Civil War, many families put away their looms as more industrially-produced woven cloth became commercially available. So, all of the lessons that I learned from Berea College and the history of home economics here at UW-Madison started to inform the way I thought about sort of production around weaving and the potential of craft and woven design. I think something that’s still unresolved to me is the relationship between that history and my own background as an artist. And so I still struggle with this relationship today between art, entrepreneurialism, and innovation, but I think somehow these things can come together, and you’ll see how I blended them in my next project that I wanna tell you about called Weaving Lab. I was inspired to think about what I could do in relationship to social practice, and ask some of my research questions in a social space. I looked back at the history here at UW-Madison and found that the weaving laboratory started in 1915. I took inspiration from that, and over a hundred years later, I created my own project called Weaving Lab: Plain Cloth Productions at the Wisconsin Institute for Discovery. I had come to UW-Madison after teaching 13 years at the School of the Art Institute, and I was really interested in the relationship between scholarship, research, and lab practices. And in this setting here at the Wisconsin Institute for Discovery, there’s a lot of public-private partnerships around tech innovation and technology, and I wanted to insert my investigations in weaving right into that context. Gratefully, I had a role model to look up to.
Here, I’m showing a slide of the artist and professor Lynda Barry, who had a project called Image Lab that she ran in the Wisconsin Institute for Discovery. And I really admired how she was blending the creative practice of drawing with thinking about the relationship to bigger questions around research and innovation and how the mind works. And so I asked her if I could take over her space, the Image Lab, for a summer, and she invited me, and that’s how I first opened what I called the Weaving Lab, within her space. So, specifically the Weaving Lab invites the community to sit at floor looms to see how they work, offering participants an entry into the process of weaving. Creating the lab gave me a space to start thinking about production of cloth made collectively. I drew much inspiration from the social energy and the utilitarian applications from the early American cottage industry and the model that I spoke about in Berea College. I had a couple points of entry into my own research. So, the first point of entry was the historical model of local production, and it asked whether access to looms as a social destination within communities might create a contemporary analog to the Fireside Industries of old, creating social connections anew. The other side of the project is conceptual and asks participants to approach the act of weaving as an end in itself, and to consider weaving in relationship to time, rhythm, meditation, materiality, pattern, and process. This is the part that falls under a term I call speculative weaving, wanting the participants to ponder and perhaps reconsider what they know about weaving through the experience and process on the prompts that I have established for them.
So, I approached the lab with a number of prompts, starting with the stereotypes or questions I had around weaving. For example, how much can be woven on a floor loom? This was a question that I had never asked before, because as an artist, I had always made individual pieces, and moved on from one piece to the next, but now, doing this social practice project, I wondered how much could we weave collectively? So in this prompt, I set up a floor loom to weave 40 yards of cotton cloth. And from that cloth, we made custom Weaving Lab lab coats. For this prompt, I positioned the question around patterns and sequence of color within the creation of hand-woven cloth. So, while I was more focused on process than the product, this loom produced a ton of fabric. You can see it’s all different, from all the many hands that wove on the loom. And once the fabric was completed, we made them into some pillows to have individual end goods that were made from this particular prompt about pattern and sequence. So, weaving is often associated with a passage of time, thread by thread being laid into open shuttle cloth. As we mentioned with Penelope earlier in the myth, she would weave and unweave every night, and the people were none the wiser because they knew that weaving took a long time. So in this particular prompt, I asked people to come and commit to weaving for one hour.
I call this project the hour towels. So, the question is how much can be woven in one hour? And I love how, in this example, these small towels sort of serve as a physical representation of time. So, here is sort of a timeline, and it wasn’t to compare, you know, who was a faster weaver, who was a slower weaver. In the end, it was just to sort of see what the accumulations of threads looked like over the duration of time of one hour. What we noticed was that everyone who wove on that loom always wanted to listen to something while they were weaving. So, the second year I ran Weaving Lab, I also wanted this prompt to be around time, but I made it in relationship to an album. So, a physical vinyl album. The weaving participant would pick the album that they wanted to listen to, one or two, and on side A, they would weave a right-facing twill, and then they’d flip the album, and on side B, they’d weave a left-facing twill. So, the textile would become a physical representation of the time they spent listening, and also of the physical act of flipping over the record. Here are some examples of the different woven works, and we tried to not only document the weaver, but the albums that they listened to along with the day that they wove.
So, I often hear people say that weaving is meditative. And so for this prompt, I wanted to set up a floor loom that investigated the idea of meditation, or weaving as a meditation. So, it was the most simple, basic floor loom, plain weave, but what we’ve produced for this prompt was, here’s all these what look like rag rugs, but I was calling them meditation mats. But we also wanted to use recycled materials, so the process involved making strips from excess materials, including denim and all the leftover muslin from our fashion program here at UW-Madison, and just making the strips itself was sort of a meditative process, because it was very slow. But as we cut the strips and wound them onto shuttles for the participants, they were given the time to just weave back and forth and discover if they found it to be a meditative process. The second year, I collected scraps from a clothing line made in Chicago. So, it was really great to incorporate secondary scraps. And I think the other meditation was on excess and waste in our fashion industry, and how we can all do better with that. Which, here we are, it brings me to the Hello! Loom itself. So, what we found, while this wasn’t an initial prompt of the Weaving Lab, what I found was that all of the participants who came in, some of them could stay, but many of them were busy and had to move on with their day, but they all were really interested.
So, I had to come up with a way to send them away with something they could do, a way for them to keep their curiosity in weaving, even if they couldn’t stay and participate. So, I had made many distributable art projects before, but this was a chance to think about how can I make something cheap and portable and accessible, and gratefully the design studies department here at UW has a laser cutter. So, my first try is there on the left; it’s quite crude. I called it, back then, a iPhone-sized loom, because I knew I wanted it to be pocketed, something that you’d throw in your pocket, just like you do with your cell phone. And you can see, it’s just a piece of cardboard, like chipboard, I guess. And even then, the tools were embedded. Eventually, the design sort of evolved to be more sophisticated to actually resemble a cell phone or a mobile phone, because I thought it would be something even more desirable than having that kind of crude, shaped cardboard cutout. So, the image you’re seeing on the left is of some of our first run being cut here at UW on the laser cutter. And then eventually when we went into production and it became more of a business, we sourced our cutting locally at a business called Routed 4 U in Sun Prairie. So, it was really important to me as we move forward to keep sourcing local, if we possibly could, and from the very beginning, we partnered with Routed 4 U, and they do an incredible job for us.
And we’re really grateful to be able to create a product not only made in the U. S. A. , but made within 20 miles of here in Madison. We used the looms extensively in Weaving Lab for workshops with children. Saturday Science was a big one, Science Saturday, and we distributed them freely for the two summers of Weaving Lab. Here you’ll see some of the ways that the loom itself works. Once you are done with your woven piece, you can insert a stand, which is something that I think is very unique to the Hello! Loom. It has the needle and a comb, all right there. The one thing I couldn’t embed was a scissor.
So, unfortunately can’t laser cut a scissors, but if you could, I would. Here are some examples that I have used the loom for. It’s largely a prototyping tool. That’s what I think of it as. It’s a space to learn. It’s a space to experiment. It’s a space to play. And I love it as a space to prototype before I do a larger project. So, that’s what the Hello! Loom is good for. Not only that, I like to think of it as a place to sort of get off your phone and engage in a physical process that could sort of bring you more of a holistic or mindful moment, ’cause I think we’re all moving a little too fast through the world.
So, having a connection with materials and process I think is a good thing, any time you can find it. So, let’s talk about the name; why Hello! Loom? So, I was inspired to name the loom Hello! Loom, because, first of all, I wanna introduce you all to weaving. I want you to introduce yourself, hello, loom, hello, weaving. But also I was really inspired by the relationship to hello, the phrase “Hello, world,” which was used in 1978 by Bell Labs computer scientist Brian Kernighan, who wrote the text message that said “Hello, world” using the computer program. So, it was one of the first pieces of text used, and I am really interested in the history of the computer technologies. So it seemed like a good relationship between the loom and messages. And so that relationship between computers and looms might be confusing now, but I’m gonna go way more deep into why they are related as processes and as binary systems. The other link of course is the size of the loom. So, I was really inspired by the portable technology, the portable computer in your pocket that we all carry now, which is the cell phone. And so those are the links between the loom itself and early computing, and Hello! Loom, the message.
Let’s talk a little bit about the binary systems that I mentioned in relationship to computers and computer history. So, in weaving, we have a way of making weave drafts or the plan that you’re gonna use for weaving. And it’s a binary system. So let’s look at the place where it says a black square equals the warp up and a white square equals the weft up. So, as we introduced you to before, or as I introduced you to before, there’s the warp and the weft. So, there’s two elements, but they can combine in so many different ways to create a woven cloth. And these are showing you the different weave structure families. And so these are just three out of millions of different possibilities, but on the left you’ll see a plain weave where it’s going every other. So, the top diagram that looks like a checker board is showing you up and down, over and under of a very simple plain weave. The image right below it shows the cross sections.
So that’s what you would see if you were seeing the weft passed over and under every thread. The next one in the middle is called the twill structure. And this is two, one, twill. Two are going white, so the weft is going over, and then the black represents the warp going over. And then finally a satin. So, you’ve heard these words before. Your jeans, your denim jeans, are made in a twill, your satin dress, your prom dress, is made in a satin weave. So, they all have different qualities, but, again, it’s a binary system. And I think it’s a really interesting thing about weaving and how it relates to code in general. I wanted to show a few other examples of binary systems.
So, there’s the I Ching, there’s electricity. It’s either on or it’s off. There’s Morse code, and here it is, the weave draft. And here’s another slide that articulates a little bit better about the plain weave, twill, and satin as they interlace. So, you can see the different textile qualities to how these threads are interlacing and going over and under. I also want to point out this loom structure because I’m about to jump into what a Jacquard loom is. But before I did that, I wanted to show this weaving technology, which is from the 1740s; it’s called a crumb-machine. And I think what you can see here is that there’s these raised and lowered slats, and those hold the patterning that the weaver would weave. And so it was a really ingenious way, a system for the loom itself to hold the pattern that the weaver would weave. Next up comes the Jacquard loom.
So, most people know Jacquard weaving or have heard that word before. And so this guy, Joseph Marie Jacquard, invented or was commissioned by the French government to develop a new loom. He combined previous technologies, we don’t wanna give this guy all the credit, to create this loom. And I wanna point out that his primary technological advancement with this loom was where you see the red arrow. It’s this advancing mechanism that he made that made it so that the loom went from being a two-person operation to a one-person operation. And it really upset all the people in Lyon, France, where this was first invented, because it meant that they didn’t need to have two people weaving. So, it really eliminated a lot of jobs. So, it was a technological advancement that had a large repercussion, and people were throwing the looms in the river and they were really upset. But by 1812, there were already 10,000 Jacquard looms that had been produced in France. So, in that six-year span, from when it was first invented in 1804 to 1812, there was a ton of looms being made.
So, it made a huge difference in the production of fancy cloth in Lyon, France and France in general. So, this loom no longer called for skilled artisans, but only required manual laborers. The production of this loom was fiercely opposed by the silk weavers because it allowed for intricate patterns to be woven into cloth at the same speed as plain weave or plain cloth. So again, I find it interesting that in France, everyone demanded like fancier and fancier textiles, because that was the taste of the time. But plain weave would’ve been sufficient, right? But we all love decoration, and that’s why the demand for this loom really rose. But I bring it up because the Jacquard loom is run on punch cards, which is a binary system, as we know, and the binary system here is storing the data, right, of the pattern. So, the pattern itself that’s woven into the textile is stored in this binary coding system, where as the loom reads it, it’s either, there’s a little metal piece that either goes into the hole or doesn’t go, you know, can’t go in. And that shows whether the warp is gonna lift or lower in that particular moment. So, it’s data storage. As I say here in this slide, early data storage.
So, I love in this slide, on the left it shows the pattern drafted, and then on the right, it shows what looks like hundreds of cards that have that draft stored in them. So, that is early data storage, and really revolutionized early computing because that is what led to how we tabulated the census, for example. Early punch cards led to early computing systems. So, in thinking about having people think about code in relationship to weaving, I think about how drafts can be translated to something that you’re weaving by hand. So, this is something that generally, when we use the loom as a machine, we let the machine handle the patterning. But what I wanted to investigate is if we could slow down and do it by hand using the Hello! Loom, because I think by connecting these systems through your physical, your body, perhaps you could know the code a little differently. So I came up with a series of drafting exercises, where, in this image, you’re seeing all the different, not all the different, but many different types of weave structures that you could embed into your draft or your plan for weaving. And so you could draw it out here and then execute it in yarn on your loom. In this next slide, I pay homage to early emoji designs, which I am told were 12 inch by 12 inch square. Before we have our beautiful, amazing emojis that we use now, they were all made out of black pixels, and only 12 by 12 inch resolution, or 12 by 12 square resolution.
So here I made, I paid homage to the two of them, the heart and the peace sign hands, embedding it within a twill background. So, you could weave these emojis on your Hello! Loom. And finally, I generated some random bitmap patterns to think about, again, these binaries, the black and white, the zeros and ones, of the relationship between weaving and computer code. So, now I wanna transition to talking about the partners that I brought on to create Hello! Loom, and the patents that I had been able to get for Hello! Loom. So, becoming a business is a really difficult process on some level. I mean, some parts of it can be easy. In this sense, becoming a business for Hello! Loom was much easier than my first business because it didn’t involve any wearable technology. So that was, or external manufacturing, really, so that was a win. But I did need a business partner. I couldn’t do it by myself.
I am a professor at UW-Madison, so I have a full-time job. So I was grateful to bring on Erica Hess as a business partner. She was a former graduate student. She’s an amazing designer and has a ton of business skills that she brought to the table. Additionally, I worked with the Law School, Law and Entrepreneurship Clinic, the Wisconsin School of Business, the Business and Entrepreneurship Clinic, and the Discovery to Product Center here at UW. All of these resources became an amazing jumping off point for Hello! Loom in the business. And I couldn’t have gotten any of the paperwork or the legal requirements set up without those resources. So, I’m really grateful to all of those partners. I also had worked with WARF, the Wisconsin Alumni Research Foundation, to see if my design could be patented. So, I knew that as a laser cut element, there could be some intellectual property problems, where of course the file could be spread around and now everyone’s making the loom on their own.
And on some level, I love that idea ’cause I want it to be accessible. But on the other hand, if you’re starting a business, you have to have something protected so that you can sell a few on your own. So, I put the loom to them and asked them if it was patentable, and they came back and found that we could have two aspects of the design itself that were patentable. And so I’m really proud to have two patents held for the design of the Hello! Loom. Some other things that helped us transition from being sort of something that was distributable and free and part of a social practice project to a business itself was knowing that the loom had to be ready to go on the shelf. And so one of the things that we did for the retail situation was that we added colors and kits, ways that you could just get the loom and be ready to weave in an instant. So, here is an example of some two-color kits. Recently we’ve expanded our offerings to a few more sizes, but because we’re dedicated to the design efficiency and creating products for educators on a budget. So, here in this image, you’ll see a couple of our new sizes. The Tablo is more of the size of the iPad or a tablet.
The Baby is a small size and the Bambino is even smaller. And what I love about these new designs is that the littlest is embedded in the next littlest, or our basic loom size is embedded in the Tablo because we wanna use every efficiency with the material itself with how the tool is laser cut. And with the teacher’s budget, we have a lot of teachers from public schools that don’t have a big budget. And so we wanna make sure we give them the ability to buy the looms for their classrooms. One of the questions that we get a lot is what is it for? So, here’s the Hello! Loom, what do I do with it? And as I’ve gone over in this talk, there’s my push and pull between utilitarian and artistic purposes. To be honest, I didn’t design the loom to be made into a miniature rug for a doll house, or anything, you know, particularly utilitarian. I designed it as a place to prototype and a place to really explore materials and process of weaving. And in this slide, I’m showing a picture of the front cover book by Anni Albers called On Weaving. And this is a quote I’ll read to you about what she says about weaving. So here she says, “Weaving is an example of a craft which is many-sided.
“Besides surface qualities such as rough and smooth, “dull and shiny, hard and soft, it also includes color, “and as a dominating element, texture, “which is the result of the construction of the weaves. “Like any craft, “it may end in the producing of useful objects, or it may rise to the level of art. ” So, this quote kind of sums it up for me, that it could be either or. Perhaps it could become something utilitarian, but also perhaps it’s an exploration of all of those other things, color, texture, interlacements. I think that transitions well to like how have people used it? So, one way people have used the Hello! Loom is for exhibition. Here, I was able to go to a residency in Joshua Tree, California, and I was with other weavers. So I suggested that perhaps we all weave a project on the loom and we do a small pop-up exhibition. So, here’s a sampling of what the other weavers came up with for this short-term pop-up. So, I love that with the stand, you have everything ready to go, and you can just have your exhibition within a day. I’ve also used it within the context of international Weaving Lab projects.
So I was able to, in 2019, bring the project to Oak Park, Illinois, Oslo, Norway, Copenhagen, Denmark, and Gothenburg, Sweden. And as the show traveled, it became an important way, not only to run Weaving Lab, but to think about how to engage the local weavers. So, fortunately, the first time I went to Sweden on a research trip, I met this weaver named Sofia Hagstrm Moller, and she currently lives in Denmark, but I reached out to her to help me not only with Weaving Lab, but to meet some other Danish weavers and to see if I could get them to engage with Weaving Lab and learn more about their own research practices in relationship to weaving. And so Sofia became a assistant within the lab, but I also relied heavily on my assistants from UW-Madison, both undergrad and graduate students, Kat Bunke and Erica Hess. And they helped me run all aspects of the lab for two-week runs in each of these locations. So, it was an incredible, immersive experience. Here you’ll see, these were a bunch of French people that came to Weaving Lab in Copenhagen and engaged on the Hello! Looms for better part of an hour, having a great time. We were able to engage the local Danish weavers when the Weaving Lab project went to Copenhagen through Sofia Hagstrm Moller. As a weaver there, she had connections to all the other professional weavers. And I said, “Do you think if we sent them Hello! Looms, “they would send back some of their own examples and research within weaving?” And so 40 weavers participated.
They all brought their Hello! Looms to the exhibition, and we were able to have this mini pop-up exhibition within Weaving Lab. And what I loved was that it consolidated their work into this really small format, but it also gave us a chance to really profile 40 different individual weavers in one space, which if every weaver had a full-size piece, we would never be able to do that. So, some of the feedback I got was that they had never all been in a show together. So, I really loved that Weaving Lab could bring all these Danish weavers together to reflect their work in one place and one time, and hopefully inspire the participants within Weaving Lab. Here’s some examples of what the Danish weavers presented. There’s projects that incorporate linen, mesh, gold. Some people burned the loom itself or gave it a patina, rainbow colors and braids. I mean, what people came up with was really incredible to see. This year, in 2022, earlier in the spring semester, we had a exhibition of this same work here at the Lynn Mecklenburg Textile Gallery at UW-Madison. So, it was really exciting to be able to pack up all of those looms from the Danish weavers and bring ’em over to the U.
S. So, I love sort of the portability of it, making it really easily distributable internationally for exhibition. We also, in that exhibition, incorporated a place for participants to weave if they wanted to experience Hello! Loom. And in the background here, you’ll see a video of the Danish weavers talking about their own work and production that they had come up with on the Hello! Loom. Hello! Looms are used a ton for workshops and education purposes. So in that case, we try to make as strong of materials as we can, including worksheets and video tutorials. On this slide, you’re seeing a huge range of videos that we come up with to support people both on YouTube and our own website. So, if there’s a new skill you wanna learn or a way of weaving, just request it and we’ll hopefully make a demo or a video tutorial that we can share with you. It’s been used in universities across the country and a few around the world. So, here it’s being used at Iowa State University and Cal State LA by different professors.
One’s in a technology position and the other in textile history. I love that the textile historian can incorporate actual production in her class, because I think you can’t only learn weaving history, you have to learn through making. So, the fact that she’s able to do that with a small loom gives me a real thrill. Here, you’re seeing the loom being used in a paper-making class, where not only is it used with a paper thread, it’s then being dipped in a vat of indigo. Here it’s being used in the Design and Craft Museum in Gothenburg as part of a Weaving Lab project. But I think one of the, oh, and here’s an example of workshops being led by Sofia Hagstrm Moller in Denmark. So, she’s come to use the looms a ton by request for workshops all over Denmark. And she developed this specific workshop for us, which is something she taught here at UW-Madison this past spring semester on weaving gradients. So, I love to do these collaborative projects with other weavers to see how they can teach their processes on the loom. Here’s a long list of institutions that use Hello! Loom.
I’m very proud of this and hope that we can expand to even more educational venues. But I think the best way to see what people do with the loom is to look at social media. So, here I have weavers on social media, and I gathered these shots from Instagram, where people tag Hello! Loom, and they show us their best work. Here is someone who’s just using part of the weaving surface, right, not even the whole loom, and creating a series of bracelets, woven bracelets. Weaving pine needles, weaving tapestry, weaving two layers, painting the loom purple and red, and weaving a bounty of colors. Just so thrilling to see how all the different people are using their loom to create ideas. So, that gives us a lot of joy. And most recently, we got this slide from a woman in Canada who uses the loom to weave the tiniest little clothes for these tiniest hand-carved dolls. And we just were over the moon with that new, recent development. And she’s a huge supporter.
So, that was really fun to see. So, what is next when it comes to Hello! Loom? Well, we are continuing to make new sizes of looms. We wanna make new kits that engage people in different types of materials and technologies. We’re excited to make new workshops, to support people as they learn these new ways of weaving and how to use new materials. We’re excited to have new vendors, near and far. I mean, we do the best we can to connect with outlets, but I feel like potentially every yarn store in America should have Hello! Looms available. We’re competing with knitting and crocheting, so we really gotta work for it. Looms are not accessible. Floor looms are really expensive. And so I hope the Hello! Loom can be a starting place for a lot of weavers around the country and around the world.
And we’re also excited to have new collaborations, like other weavers can come up with tutorials and workshops that they can create on the loom. So, a lot of big things coming, just need a little time to make ’em happen. I’ve shared with you a ton about Hello! Loom today. I hope I have answered all your questions and more, because I’ve told you not only about Hello! Looms, but about weaving history, loom history, technology, innovation, materials. It’s been a pleasure to be with you today. I’m so grateful to be invited, and thank you for listening.
Search University Place Episodes
Related Stories from PBS Wisconsin's Blog

Donate to sign up. Activate and sign in to Passport. It's that easy to help PBS Wisconsin serve your community through media that educates, inspires, and entertains.
Make your membership gift today
Only for new users: Activate Passport using your code or email address
Already a member?
Look up my account
Need some help? Go to FAQ or visit PBS Passport Help
Need help accessing PBS Wisconsin anywhere?
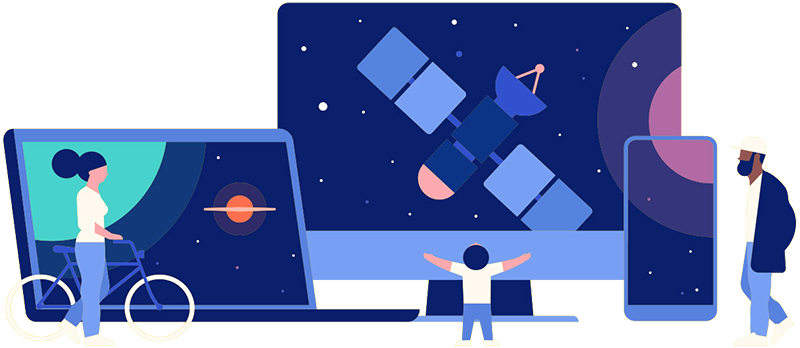
Online Access | Platform & Device Access | Cable or Satellite Access | Over-The-Air Access
Visit Access Guide
Need help accessing PBS Wisconsin anywhere?
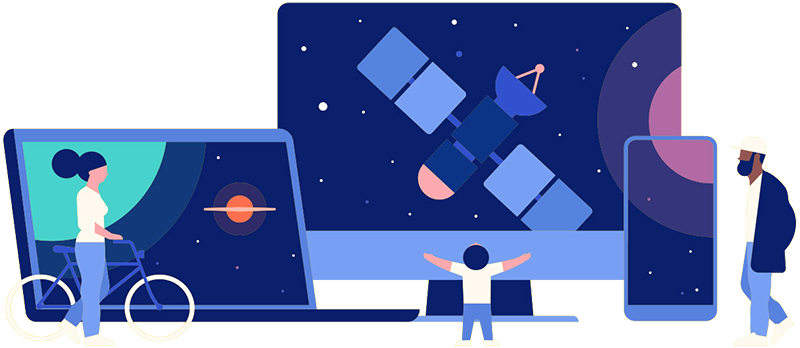
Visit Our
Live TV Access Guide
Online AccessPlatform & Device Access
Cable or Satellite Access
Over-The-Air Access
Visit Access Guide
Follow Us