– Tom Zinnen: Welcome everyone to Wednesday Nite @ the Lab. I’m Tom Zinnen. I work at the UW-Madison Biotechnology Center. I work for the Division of Extension there. And on behalf of those folks and our other co-organizers, PBS Wisconsin, the Wisconsin Alumni Association, thanks again for coming to Wednesday Nite @ the Lab. Tonight it’s my pleasure to introduce to you Lennon Rodgers. He’s an electrical engineer, and he’s the director of the Grainger Engineering Design Innovation Lab. He’s gonna be talking with us about engineering, innovation, and invention in response to COVID.
– Lennon Rodgers: Well, thanks, Tom, for that great introduction. I’m super excited to be back here and talking to you guys at Wednesday Nite @ the Lab.
I thought I’d kick off my presentation by giving you a brief overview of some of the more impactful projects that we worked on. Mainly, not to keep the suspense going too long into the presentation, but the first one was the Badger Shield. And it was a face shield, and about 40 million of those have been made. It’s really hard to predict, but that’s kinda the best number that we have as an estimate. Another project, which I’ll talk more about, is the Badger Shield+. And so about 100,000 of those have been made, and it’s essentially a more enclosed face shield. And the third one was more recently, and it’s called the Badger Seal. And it’s essentially a device that provides a seal around a three-layer disposable mask. And about 10,000 of those have been made so far. I also wanted to highlight just specifically kind of our role as a university.
Our primary role was to iteratively design, prototype, and then test with users various PPE designs that we worked on. And it was in close collaboration with one or more manufacturing partners, and often with UW Health. At the end of most of these projects, the result was an open-source design, and it was ready to be mass-produced by one or more manufacturing partner. In each case, at least those three that I just showed you, we worked with a manufacturer. And in most cases, all of our designs were tailored to be for the do-it-yourself’er so people at home could make them themselves. And so that’s something I’ll talk about a little bit. It was a focus that we had on trying to make a design that could be replicated not only by manufacturers, but also by individuals. Well, those were just a few projects that I showed, but I’m also gonna highlight quite a few of the other projects that we worked on over the last eight months, and I’ll go in more detail for each of these. But really, I just wanna tell the story. And the story is really about a group of people, and I’ll list the people kind of as I go along, and I’ll also list ’em at the end.
And it’s a very large number of people across Madison that were all working together in a very collaborative setting, all remotely for the most part, but really focusing talents and resources to help others. So it really had that sense of people just wanting to help, to help out where they could, and it was a very unique time for my life, and I’ve certainly never experienced anything quite like it. But at the end, the most important thing from my view is really the impact, and I tried to mention those numbers at the beginning. You know, it’s encouraging for me every time I see images in the news. You’ll see pictures like this, I took them from CNN and New York Times and others, and you’ll see the Badger Shield. You’ll see it out, having an impact, helping people, and that really makes me feel great and knows that what we’re doing here in Madison has more of a global reach. So again, I’ll be talking about each of these in more detail. But to kinda kick off the story, it really all started with an email that I received from UW Health on March 16th. And the email said something along the lines of that “We are in desperate need of PPE “and could you make 1,000 face shields as soon as possible?” So the first question you might want to know or might wonder is why would they contact me? And that’s a good question, but there was a good reason for them to contact my lab. And the reason why is that I’m the director of a lab in the College of Engineering that really acts as the hub and home for designing and prototyping more on the education side, so we have 3D printers, mills, lathes.
Really anything to do with making, we have. So that was the reason why they reached out to me. They actually reached out on an email thread to many others across the College of Engineering and campus in general. I also want us to remember though what was going on March 16th. Even myself, when I was kind of thinking about this, there was a lot that I had forgotten. It was a time where schools were starting to close, at least there were rumors of closures, including UW-Madison here. So there was just this element of uncertainty, and we didn’t know what was gonna happen. The concept of PPE or the word PPE, I was very familiar with it, being in a shop environment as personal protective equipment, but most people didn’t really know what that meant. So it was not a commonly used word at that time, which is weird to think about ’cause now it’s just totally normal for people to use that word. The other thing was the shortages.
The fact that hospitals were struggling or they would struggle with shortages. It was not widely known, and it was not known that it was a critical issue or a systemic issue that was gonna hit the whole world. None of that was known on March 16th when I received that email. And I didn’t know, and I didn’t have a sense of the urgency of it, and I’ll talk more about that. The other thing is that most of us were still working from. . . Most of us were not working from home. We were still going into the office. We were not wearing masks.
And really, life for the most part was fairly normal at that time. I think there was a lot of, again, uncertainty in trying to understand what might happen, but we weren’t really in the thick of it yet. On the personal side, I think a lot of other people were dealing with this too is that we have two kids and we heard schools were closing, which for a parent, you’re thinking childcare. How are you gonna manage that situation? So on March 16th, that was top on my mind. My wife is an anesthesiologist at UW Health, and so that was another thing on my mind in terms of what was it gonna be like for her? How are we gonna manage the childcare? There was a lot of frontline worker discussion going on in the news. So that night, on March 16th when I got home, the main discussion with my wife was about childcare. And then, when the kids went to bed, it kind of migrated more towards anesthesiologist life, what that’s gonna look like. And in the midst of that conversation, I mentioned this email that I’d received from UW Health. In some ways, I received those types of emails every once in a while of someone asking for some help, maybe fabricating something or some ideas that they have that they’d like to fabricate. So I didn’t necessarily think that much of it, and so I kind of mentioned it to my wife.
I said, “Well, I received this email “and it was from UW Health and it’s kind of weird. “They’re asking for 1,000 face shields, like, “do you really think they’re running out of PPE?” And she said, “Yeah, I think we actually are. ” She said, “I heard about this myself. “I’ve kind of started to see it. “There’s been discussions about this in our department. ” And so the general sense was that it is serious, and she also started telling me a little bit about why they use face shields, the risks for her when they’re gonna be putting a breathing tube in COVID patients, and just the general, educating me in general about what the situation might look like. So it kind of went from a random request to something that became more personal. And so that night, I kinda focused and channeled my energies into what I do, which is making prototyping. And so I went to Home Depot and this was kinda the result of going through the aisles of Home Depot, going through the craft store, trying to just do a quick prototype, which is kinda normal for what we would typically do with a design cycle. And so after a few hours here at the Makerspace, which is where I’m at now, this was the first prototype.
Kind of a Frankenstein, putting together some of the components that exist, combining with some custom components that I made on the laser cutter. I took that, went back home, and I showed it to my wife, and she put it on and she’s like, “It’s way too heavy. ” So that was kinda the first user feedback that we received. And she gave me some other very useful insights. But you know, I knew right away the next morning that there was no way I was gonna do this by myself, so I reached out to a handful of people. Actually, I think the similar number of same people that were on the initial email from UW Health combined with some others, and sent them a link to my prototype and said, “UW Health really needs our help here to create 1,000 face shields,” and very clearly early on, two partners just stepped up. It was Delve, which is a design consulting firm in Madison, and Midwest Prototyping, which they’re based just outside of Madison. So if you know these two companies, you know that they are the superstars you want on your team. So it was very fortunate for them to also step forward and offer their help in a full throttle sense. So Jesse Darley is shown on the right there.
He is a mechanical engineer. Brian Ellison is on the left and he’s from Midwest Prototyping. I’ll tell you a little bit more about them as we go along. The unique thing, I think, at that time we started remotely communicating and trying to do some prototyping. Part of it was done here at the Makerspace, part Jesse was doing it at his home, part was being done at Midwest Prototyping. All remote ’cause at that time we didn’t even know if we could really even get together, even if we were wearing masks. There was a lot of uncertainty there. I was making runs back to the craft store, getting more foam heads like the ones you can see behind me. You know, getting fabric, getting elastic. And it was a little eerie, to be honest.
The stores were empty. Very quickly, things were emptying out and it was pretty much me and the workers and that was about it going through the aisles. So that’s what I have a picture there of, just an example of going inside the craft store. Kinda the state of do-it-yourself face shields at that time were kind of interesting. We started doing some research into what exists and that’s kind of the normal first step is understand what’s out there. And clearly the traditional supply chain was completely broken, so there was no option to go out and just buy the face shields that exist. So a lot of organizations really across the world, even over to Italy were coming up with different designs for face shields because it wasn’t just UW Health. I mean, there was a huge need for face shields. Most of them were 3D-printed, and so that’s what this picture is. This is probably the most popular one.
I think it was one of the first ones that I saw. And so Jesse and Brian and I looked at that face shield and we looked at some other designs and we really wanted to 3D print them. In fact, we could understand the appeal. It was, it was very appealing from a designer’s perspective to use 3D printing. It’s an awesome tool and we use it a lot for a lot of different things. But we kind of all knew that it might not work, and the reason why is that it’s expensive equipment and it’s also expensive materials if you start thinking about large quantities. And if you also go back to kinda what I said before, is that we knew that we wanted a design that could be easily made, and in hindsight, it was critical that it could be made by pretty much anyone. The other problem with 3D printing is that it’s very slow, so it takes a long time, relatively speaking, to make even one of these face shields. And then the other thing, which may or may not be the case depending on the design, is that they can be kind of uncomfortable. It’s a hard plastic on your head.
So we kinda went back to what we’ve been trained to do, and our approach was basically just kind of ignore that for the most part. We knew that that probably wasn’t the right approach for the reasons mentioned, but we just really wanted to go back to the basics, focus on user needs, go to the hospital, understand what they needed, what was already out there, what did they already use, create as many prototypes as we can and really focus on mass production. We had a sense that it wasn’t just this 1,000. It was going to be a lot more, and we wanted to be able to produce a design that could be made in the millions. So this the result of our few days of prototyping and testing, and we called it the Badger Shield. And it had a few key strengths. It had a very simple design, so it could be mass-produced or made by individuals very quickly. There was really no need for specialized equipment, so you don’t need a 3D printer. You really just need some household items like scissors, stapler, and a ruler, and some cutting tools. Really basic stuff.
The materials were pretty easy to source in large quantities. I’ll talk about later that even though it’s fairly easy, when you get to a certain scale, the supply chain becomes a challenge. What we received from feedback is that it was quite comfortable; we felt that ourselves. My wife definitely gave it a thumbs up. It was a lightweight. That was one of the things that she was critical of the first design of. And the foam was quite comfortable on the forehead, so those are perks. It was very cheap. It depends on how many you make, but it can be made for tens of cents and it can be made up to just over a dollar if you’re doing it yourself in small quantities. And really, what we wanted to do is we just wanted to improve their existing face shields.
So it was something that they were kind of familiar with. Even though we feel we improved the design, it was fairly familiar to them. So I just want to show you the actual face shield. This is it here. And as I mentioned, it’s a very simple design. It really just has a few pieces. It has a clear plastic shield in the front. It has some elastic that’s stapled on there, both sides, and some foam. So like I said, it’s extremely lightweight and you can barely feel that it’s on your head. So after I guess, about nine days we had a lot of prototyping and it took a little while to establish Midwest Prototyping, their assembly line, ’cause they were making them.
We delivered, or Midwest here, Brian Ellison’s delivering them to UW Health, 1,000 Badger Shields. In hindsight, it was extremely quick. In reality, there was a lot of other things going on during those nine days, and so I’ll talk a little bit about that. We knew that beyond just delivering the 1,000, I mean, I guess, I personally knew, I was driving home from Midwest Prototyping and it just came to me very clear that it was gonna be much more than just an open-source design or even just the 1,000 for UW Health. So I contacted the operations manager here when I was driving home and I was like, “We have to get the design online. “We have to start connecting manufacturers. “We have to start connecting hospitals “and build the supply chain and things like that. ” Those are kind of those three bridges, it was beyond that first 1,000. So the first bridge was connecting the manufacturers to an open-source design. The second bridge was connecting manufacturers to a supply chain.
And the third was connecting manufacturers to hospitals, the users, the customers, the ones that were in need of the face shields. So I’ll step through each three of these aspects, these bridges just briefly. So the first was kind of the dissemination piece. It was the open-source aspect of the design. So Jesse Darley created this engineering drawing on the left with a bill of materials which lists out all the different materials that are needed and links on where you can buy them. He and Brian Ellison then put together this list of step-by-step images, which are shown on the right, of how you would basically take all the different raw materials and that you would end up with a face shield in the end. And then we created this website and posted the design on the website. The second bridge was that connecting manufacturers to supply chain. And so what we did for this is that we realized that if you want to start scaling this up in large quantities, getting large sums of plastic and elastic and other things, it’s a little tricky, and especially if you’re doing it in a very short period of time, and especially if you’re entering an area that you don’t normally. .
. if you don’t normally make face shields, you don’t even make medical equipment, which is what we saw. There were a lot of people that were entering this arena that were totally pivoting from something different. So we wanted to help them create the supply chain essentially and make it easy. So on our website here, you can see it on the left, is that we created a database where suppliers of PET, which is the plastic, the foam, and the elastic could come to our website, enter their information, what they have available, their contact information, data sheets for their products, and then that could be made viewable by the manufacturers that were making the face shields, so it’s kinda the assemblers of the face shields and the people that were cutting the plastic and things like that. So this was extremely, like I said, a critical bridge that we had to create. The final bridge was really once a manufacturer has a finished product, how do they then know where to send it? And that was a real issue that we talked to early on with a lot of people that were making face shields. They didn’t know who was in need. So this was largely initiated by a graduate student here in my lab named Rebecca Alcock. And I contacted her and I kind of explained the situation and she really ran with this.
And she reached out to a professor, Justin Boutilier who she was actually taking a class at the time that was he was offering on this general area of supply chains and healthcare. So they ran with this. They created an algorithm that tried to prioritize those in most need. They had an intake form where hospitals could submit their information and based on various metrics, then this algorithm would then connect them to manufacturers that had supplies of face shields. And so this was extremely interesting in general. Justin calls it the “pop-up supply chain,” and The Wall Street Journal had an interesting article that kind of highlighted some of Justin’s work and some of our and Rebecca’s work. And he had a collaborator from UCLA, Auyon, and it addressed this phenomenon called pop-up supply chain. Well, after and in coordination with these three bridges being built, the Badger Shield design, this face shield really did go viral, and it evolved with a lot of different people kinda running with it with minor tweaks and really did what we had hoped. So Ford Motor Company contacted me early on and they started using the design. This is an article shown on the left by Wired magazine that highlights some of our work, some of Ford’s work.
And Ford essentially had totally retooled an assembly line and put their workers at the task of creating these face shields, so it was really neat to see. And they used the Badger Shield design. They made, like I said, some. . . some minor tweaks to it, and they were very appreciative. And we collaborated with them for a month or more on their effort and just what in general was going on. There were other companies, Intuitive has an article. They reached out to me. I think in this article they said they made a million.
That’s the company that makes the da Vinci robotic arm. John Deere mentioned the Badger Shield as part of their effort. Kohler contacted us. Those large producers were super interesting. What was, I would say equally if not more interesting were the smaller manufacturers, the smaller companies that were making them, and I’ll give an example. My parents had heard what was going on with this effort and so they called me and I was talking to them and they mentioned, they said, “Well, you know, I heard that the local hospital “in my hometown, Sterling, was also in need of face shields,” and they wondered if there was any way that I could send them to the hospital. And I explained, well, we’re not really making the face shields. We’re really just trying to support through those ways that I mentioned to you guys just a second ago. And I said, but please have the hospital in Sterling, the hospital that I was born in, have them send in a request to our intake form on our website. And so, like I said, I felt kind of bad because I couldn’t, I knew it wasn’t the right thing to do to try to do these favors, and we were trying to help those in most need.
That’s what Justin and Rebecca’s algorithm was doing was trying to prioritize areas that were in most need at that time. And so I got off the phone with my parents and I went back and checked my email, and I had received an email from a factory, a small factory in a small town called Wahl Clipper. And the engineer from Wahl Clipper had said, “Hey, I saw your design and we’ve made,” I think they said something like 1,000 of them already. They had modified the design actually fairly significantly. They had really run with it in a cool direction. I was really impressed. And he’s like, they have these face shields and it just so happened that Wahl Clipper is in my hometown. It’s in Sterling. And so I said, “Hey, this is great. “Please contact the local hospital.
“They’re interested, they need face shields. ” I think that was a really good example, just totally random of what was going on across the world really. Is that local companies were making these face shields, they were connecting to the local hospital, and it was a much more effective way to work. Because these companies could respond quicker, they could be a local source as the supply chain is kind of fragile, and it just is a really good way for community engagement and having those kind of partnerships. So like I said, it went viral, and I think from big to small we saw the Badger Shield being made. And in just over one week, the Badger Shield effort had spread to half of the country. So this plot is data taken from our intake form. It’s not perfect. It’s probably an underestimate for what was going on, it almost certainly is, but it shows that within seven days, hospitals were active in 40 states across the country, and in 39 states, we had some presence of a factory making the Badger Shield or someone making the Badger Shield. And this is just another plot kinda showing the same idea.
Is that in about 19 days, they were approaching 600 different participants in making Badger Shields. And like I said, the numbers vary. It goes from Ford, who was aiming to make a million, they’ve said that they ended up making I think 20 million was in a recent article I saw, to Wahl Clipper. You know, they were the smaller factories that were making it just for their local needs. So here’s a summary of those three bridges that I mentioned. And I think it’s really interesting. This is a bit of a reflection, but why were these bridges needed? And I think from the open-source side of things, it really allowed companies to save time. It lowered their investment and their risk. It allowed for crowdsourcing and iteration improvement of the design, and then it allowed for standardization. That really impacted the supply chain, because if they’re all working around the same design, the supply chain can adapt to what those needs will be.
In terms of the supply chain, it saved the companies time, it reduced effort, and it drove competitive pricing. I mean, by posting all the supply chain vendors on our website, it allowed the manufacturer to go and get competitive bidding from those different companies. If they wanted to, it was their choice. And then from the manufacturer to hospital side, again it saved time. It allowed the manufacturer to gauge demand. A lot of companies would contact us and say, “How many face shields are needed?” And we really were not able to help them much, but we were able to just show them the data that we had collected as a factual piece of information that this is what hospitals are saying that they need. It provided them with immediate customers through that matching algorithm that I mentioned that Rebecca and Justin had made. And then it again drove competitive pricing. Hospitals could go out there, see who was making face shields and it could help with the market forces. So that’s, like I said, the summary of the Badger Shield, and everything I’m gonna kind tell you now is what kinda happened after that.
So this is still probably in the late March/ early April timeframe. We started getting approached by UW Health for slightly different needs, and so I’ll tell you a little bit about some of those. The first were derivatives of face shields in some ways. Is that, here’s Dr. Bentz who approached us and said, hey, he really likes the face shields, but he’s having some issues with some of the optics that he wears when he’s in the operating room. And so here’s an example here of one of the early prototypes. But we had multiple iterations with Dr. Bentz. He would come and drop things off, we would send them and leave them outside of our door. And we never actually met in person, which is kind of funny because again, the general sense was just to really avoid other people.
But here you can see this face shield, it kind of goes below the optics. And so the surgeon can be protected, the plastic covers as much of their face as possible and then they have glasses. And so this is an interesting design that we actually are pursuing patents on right now with WARF. Here are just some sketches. It shows you a little bit better detail of what they were of the one I just showed you. And then there’s one on the right there is one for an ophthalmologist. They have this different type of optic, so there were a handful, maybe three to five different designs that were largely done by Karl Williamson here. He’s the shop manager at the Design Innovation Lab or the Makerspace. And they were able to go in the field right away. It took probably a month, but they’re still being used now.
So next, I’m gonna show you a video that was done and I think it kind of speaks for itself. And it’s one of the next projects that we worked on. [gentle music] – Dr. Scott Springman: This is pretty much an unprecedented event in my lifetime. We learned early on when the pandemic was beginning that the hotspots ran out of personal protective equipment very rapidly. When we’re in a very high-risk procedure, such as when we place breathing tubes in the patients that are struggling to breathe and very sick with COVID-19, we would have to have something that protected us the most. A PAPR is a powered air-purifying respirator. One of the components is the actual part that one puts over your head, and the other part is the motor that takes purified air using a filter and then pushes it into the hood that you’re wearing. So when I was put in touch with the UW Makerspace and Jesse and Delve, I was very gratified that at least I could have some input into what was being made and what kinds of things would be useful for us to protect ourselves. – Man: A little too tight against the face? – Yeah, I would say.
– Yep. – I feel the airflow more in this one. – Man: Okay. – In working with Delve and Jesse, we really tried to recreate, kind of reverse engineer existing PAPR hoods. We went through several iterations of the prototypes, and I feel very confident that the final prototype will do the job. It’ll protect us and it will keep us as safe as possible. Working through the design, I think a couple of the major points were that it would be easy to wear, because providers may be called upon to wear it for extended periods of time. That we could actually see what was going on through the face shield, and that it was a design that we felt confident that it would protect us. One of the challenges in all of this is that there is no standardization really on how the blower motors connect to the hoods themselves, and so we had to consider and Delve had to consider how to make sure that the hoods when they became available could be used in almost any kind of system. So I was pretty impressed with the idea of 3D printing these connectors and allowing us to have adapters so that we could use it with any kind of hardware that we would be using for the hoods.
So having the PAPR with the filtered air really helps us feel as though we can concentrate on taking care of the patient and not worrying about the fact that we’re putting ourselves at risk. I and my colleagues are very appreciative of the effort that went on in this development because it’s really helping us be safe while we’re taking care of patients, and the fact that the design team really went out of their way, they spent their time, their resources, their energy pretty much nonstop in order to get these done. So thank you very much to everyone. – Scott Springman was a key partner in this effort, along with you’ll see Jesse Darley on the right and Brian Ellison and Corin Frost and Karl Williamson is there. There were a lot of people working on this, and as Scott described we wanted to develop a universal PAPR hood. And so here are some pictures. I think what was interesting is that just the lockdown element and some of the restrictions and constraints we had. The picture in the middle and a lot of video footage was shot in the back of the hospital at the loading dock by the dumpster. Meeting Scott, Jesse was going there. I was showing up, Brian was there, and just testing multiple iterations, multiple trips back to the loading dock because we couldn’t go in the hospital, so we were meeting Scott and he was testing it along with other clinicians.
Then the result was what we call this universal PAPR hood. And it has this universal fitting on it that can be used by multiple PAPR blowers, and then this was the actual hood itself. And like our other designs, we created open source documentation. This is largely credited to Corin Frost. And we published this on our website and made it available with a lot of detailed engineering drawings that could be 3D printed and fabricated. You can see that the complexity is going up quite a bit. So a PAPR hood is an extremely complicated device. And it actually probably was a bigger design and engineering feat for sure than the face shield. So the next project I just want to highlight, I have behind me here. And we got approached by UW Health shortly after that and they said, “Well, we received some of these,” what are called the hood covers, they’re PAPR hood covers.
It’s the same idea as what I just showed you, but it’s kind of a more compact version. They said that, “Well, we have 1,000 of them, “but the problem is is that “they came from a government stockpile “and they have the wrong fitting on the back. ” They have this kind of odd fitting that doesn’t fit into their blowers. And so we worked to create this 3D printed fitting. Most of the work was done by Karl Williamson here, but also I was involved and Jesse Darley was heavily involved from Delve. And here’s this 3D printed fitting. And it, basically what it does is it just can snap inside and it’s like, you go from 1,000 unusable PAPR head covers to 1,000 completely usable head covers, so this was a huge win for the hospital. We also made this available if other people were interested and the 3D printing was done all by Midwest Prototyping. So they have very large capacity to 3D print, so finally we had a large amount of 3D printing after all. So this was probably, this was one of the next projects, and this was probably the April/May, getting into May timeframe.
And Karl and I at this point had a little bit of time on our hands in some ways. The campus was still empty, and we just wanted to find other areas where we might be able to help. We were seeing in the news that meat packing plants were starting to have outbreaks, factories were having issues, and so we came up with this design called what we called the Compact PAPR, or the ‘PAPR Go’ was an early-on name. And it’s this one right here. And it’s essentially the same idea is as a PAPR. It’s a positive pressure device, meaning it brings in filtered air with a blower that’s in there and then it circulates air, and then the air is kind of discharged around the outer edges of the face shield/PAPR cover. The idea is that everyone would be wearing these and so then you can kind of let air escape ’cause everyone has positive pressure devices on. So we were really pumped up about this and Karl and I were super excited, and so we showed it to the hospital. Their basic feedback was they really liked the idea that someone’s able to wear this and kind of see their face, and that was part of our desire too. But they said, “What we’d really like is something “that kind of looks like a face mask with a cut out of it “so you could just see their mouth.
” And so that was one of the early-on prototypes that you may be able to see behind me up on the board, of basically just taking a traditional surgical mask and then cutting out and putting in plastic so someone could see the wearer’s face or their lips for when they’re trying to speak. Maybe if someone’s hard of hearing or something along those lines. Well, that kicked off a month or two long effort really with UW Health. This is Nathan Wilke shown here. That’s Karl in the upper right. Karl Williamson is in the lower left. We just prototype after prototype after prototype after prototype. A lot of them are captured up on the board. Not all of them. We have bins full of other prototypes.
And it had that same iterative loop that I mentioned at the beginning, where we would do some designing, we’d do prototyping, we would do testing, and the testing is shown in the lower right-hand corner with clinicians, and we did a lot of testing with clinicians. And Nathan took them to all different types of clinics across Madison and I think even just southern Wisconsin, and we received tons of feedback, a lot of it very critical, which is good, and positive, negative, everything, and that was good. That drove our design to improvement. And in the end, what we came up with which is called the Badger Shield+. And it’s essentially a lot of the same components as the Badger Shield, the face shield, and that was very intentional for the supply chain reasons I mentioned before. But what we did is we added some fabric around the bottom side. It sealed it up and had a better coverage in terms of infection control. And then there’s an optional magnetic fan that goes on the inside. And this can. .
. There’s magnets on that and it snaps in and you can either mount this fan or not. I designed. . . This was in collaboration with Midwest Prototyping. Karl Williamson was involved. I was very involved and I did most of the design work for this blower, and then reached out to a company through some other partners called Matrix Product Development, and they really helped refine this design. But I personally never thought that people would wear the Badger Shield+ without the blower. I thought it would be too stuffy, but it ended up being that the hospital actually, the initial versions and the ones that have sold the most are just the Badger Shield+ by itself, which is shown on the picture on the left.
So the Badger Shield+, when we released it, it was kind of at a unique time. It was around the July timeframe, and I’ll talk a little bit at the end why I think it took off the way that it did. But essentially, in 72 hours we released our design. It was again an open-source design. We received interest in 20,000 Badger Shield+ units. So that was just, like I said, in a few days. So the demand was extremely solid. The next project I just want to highlight was one that was done by David Rothamer and Scott Sanders, and I’ll kind of explain how I got involved partway through their effort. This is in the midsummer timeframe or early summer, and now the planning was all around going back to school and how would we open up classrooms and how could we do it more safely? So Scott and Dave took a classroom and they instrumented it as shown in this picture here with quite a few mannequins. And the mannequins were kind of sophisticated.
And I won’t go into detail on what they were doing, but the bottom line is they were trying different types of masks, different types of PPE, different types of HVAC, the ventilation system settings, and they were trying to understand which type of face coverings, which type of HVAC settings would, how those would impact the aerosol count in the room and also between the different mannequins. So I’ll– What I’m gonna do here is just show a video next that was put together by Professor Scott Sanders, and I think it really does a good job highlighting some of his work not only in this classroom, I’ll get back to the classroom in a second, but also just with the general topic of face coverings. Because Scott also did a lot of work with more of a lab mannequin, a single mannequin, trying different types of face coverings. [upbeat music] So when Scott was doing a lot of his tests, he and I were having a conversation and he said that the tests were showing that if he would tape around the outer edges of a three-layer disposable mask, the filtration characteristics were extremely good. And so I thought to myself, there has to be a way to seal around the outer edges of a mask without using tape. I mean, there had to be a solution. So the result of Scott and me collaborating for a few days is what’s shown here, which is called the Badger Seal. And the Badger Seal, essentially what it does is it takes a three-layer disposable mask and really utilizes the good filter material characteristics of the mask and it provides a seal around the outer edges. So here is the Badger Seal taken off. And it’s actually very cheap, if you could catch the trend.
I mean, that was a very important part. Just has a few pieces. It has some elastic cord. This green flexible material is actually a gardening tie for tomatoes. And so when I was going through a lot of the prototypes, I just ordered all kinds of different types of material and this was one of them, and it just seems to work the best. It can really flex, it’s very soft and comfortable. And then the garden tie here goes into a clear PVC tube, and then this cord wraps around the back of the head. And so I think one of the interesting things to note here is that a lot of people looked at the N95 as kind of the golden standard, which it is, and the reason why is that it provides both excellent filter material, so it has really good filter material that’s used, but it also has really good fit around the face. In fact, if you wanted an N95 mask to work properly, you actually need a proper fitting for size and the way that it fits your face. The problem with a three-layer just normal disposable mask is that the material is actually quite good.
In fact, Scott did a lot of tests on the material, which you saw some of that information in the video. You know, the filter material was good, but as you could see, the fog would escape up around the sides, which essentially is showing that it doesn’t really provide that great of a seal or a fit around the outer edges. And what the Badger Seal does is really tries to combine the good filter material, which the three-layer disposable mask has, and it provides this good fit. People that use this Badger Seal, you know right away. You put it on, you can sense that air is really moving through the filter material as it should. So we, like I said, we released this design really just in November or maybe end of October in a large sense. And we still have a do-it-yourself station out here in the Makerspace that the students have come in, faculty/staff and made their own. We also set up a small factory to create quite a few of them. In fact, we’ve partnered with DoIT Printing Services and the aim is to make about 10,000 of them. We’ve already distributed a few thousand across campus, so it’s been quite impactful I would say so far.
Well, that’s kind of like I said, some of the. . . I would say the most impactful are the projects that at least I was most intimately involved in. I want to highlight a few other ones that I was also involved with and the lab’s been involved with, but it has to do with how the broader activities were occurring across Madison and campus in general. So this is now going back to the March timeframe, and there was just all this, you know, all this energy that people were throwing out there, willingness to help, and there was also a bit of confusion, I would say, about where should people focus their energy. And so Ian Robertson, the Dean of Engineering, reached out to Peter, Adam, Zach, and me and asked if we could kind of act as the coordinator for all the engineering effort, at least from the College of Engineering. And so we just wanted to organize everything, make sure that requests were being made through UW Health, and that they were receiving the attention that they needed, and that we weren’t wasting our time on projects that weren’t actually that useful. So we created this workflow. This flow chart’s not meant to read in detail, but essentially what it is is it has this cloud up at the top, you can kind of see the sketch of the cloud.
And the cloud was really a group of people, we called it a sandbox. The sandbox were people from across Madison communicating through a Slack account which I set up, and Slack is a communication channel that you can use to chat people back and forth and share information. And so we were all in the Slack account. There were maybe 100 people. There were a lot of engineers, people from business, and people from the hospital, and we would kick around different ideas. And once something became kind of promising, we would float it by UW Health and we would ask if it was useful. And so they had a flow of communication to vet those ideas. And then it kind of flowed on from there over to engineering and then we had this process involving UW Legal and involving manufacturing partners and so on, just to make sure that we’re all working in coordination. Like I said, we weren’t wasting time, and it was just as efficient as possible. So it actually worked extremely well, and a lot of these projects that I’ll show now, at least the next few, definitely came out of this, the flow that had been set up.
One of the first ones was more related to this PAPR blower, which is shown in that center picture there. The blower is worn around the clinician’s waist and it has a filter on it and it has a motor that kind of draws air in, and then there’s a battery that’s needed and then it connects to the hose that goes up to the PAPR hood. But the problem was is that UW Health did not have enough batteries to operate those PAPRs continuously. And so they could operate for about six to eight hours on the battery, but there was only one battery per one PAPR blower, and they wanted to be able to operate each blower nonstop. And this kind of goes to the supply chain issue, is that there were no more batteries available. You couldn’t just buy more batteries from 3M. We– The hospital contacted them, we contacted them. There were no more batteries to be purchased. And so this was a real issue because the hospital was envisioning a scenario where everyone was having to wear PAPRs, which was reality in certain places around the world. So what we did for here is that we developed this, basically an add-on battery and we used a Milwaukee Tool battery that essentially allowed the PAPR blowers to run nonstop using these swappable, just like you would your tools at home.
So that was that project. And I definitely want to give credit to Josh Roth and Erick Oberstar who were a big part of the team. This was quite a big effort, and it’s actually still ongoing. So we have units being tested at the hospital right now. Very similarly is that we wanted to develop a filter that could be universal because the filters, just like the batteries, you could not buy them. There was a limited, very limited supply of filters and the filters were needed in order to be able to run these PAPR blowers continuously. This was again largely done by Josh Roth and Erick Oberstar. And this is the idea of adding these universal filters. We actually used Milwaukee Tool filters again on this case and had a 3D-printed enclosure that allowed the use of these other filters besides the 3M ones. Another project was going on around this time, and it has to do with keeping physicians safe during things such as intubations where there’s a lot of aerosols being admitted by the patient.
So this was a project that we got involved with, but it was mainly led by Sector67, which is kind of a community making space on the east side of Madison, and it also was in collaboration with UW Surgery. So Dr. Le was really driving this and he was that clinical feedback that was received. Professor Tim Oswald in mechanical engineering, really from the beginning, he got very interested in N95 masks and the question of if they could be thermoformed. So a lot of interesting work that Tim was doing around those masks. Dave Rothamer was working on filter material because if we wanted to be able to create any PPE, new, novel PPE, we needed to go to other filter sources because the filter material was actually the limiting, one of the more limiting pieces. And like a perfect example is this Badger Shield+. You know, it has this fabric underneath, and we had to make sure that it had sufficient filtration characteristics, and so David Rothamer helped us with that. He was helping a lot of people. He was really helping out in a big way with all things related to testing filter material.
Beyond Madison, there was a whole ‘nother interesting dynamic and it really had to do with a global effort, largely led through by Rebecca Alcock in our lab and the lead engineer for Engineers Without Borders. We also partnered with the United Nations Development Program, and there still is a lot of activity around this area of trying to not only help meet the needs of our country, but also globally. And so this is just some examples shown here on the slide of some of the early-on work done in Guatemala, but this has been a huge effort. Again, it’s trying to make sure that we work with them on our open-source designs, we help them source materials and things along those lines. So I’d like to just close with a few points of reflection. Some things that have kind of come with time as I kinda reflect on these projects that I mentioned. And one thing that’s interesting is that those three designs that I mentioned at the beginning, the Badger Shield, the Badger Shield+, and the Badger Seal have certainly gotten the most interest in terms of number of units produced. And it’s interesting to note that they came online or they became very of high demand when there was some kind of fearful event, or most of it was real, where people became fearful and they became concerned with either their health or the health of people in their community. So I’d like to kind of go through each of those and give my own thoughts on possibly why there was such a large demand and what was kinda going on at those times. So as I mentioned, the first one was the Badger Shield back in March and April, and the demand really initially at this time came from hospitals.
So we were primarily focused on meeting the needs of hospitals, healthcare facilities, and the events going on at that time were happening in the outbreaks in New York and Italy and everyone including you, I’m sure, saw those happening and unfolding. And the hospitals saw them too, and they were looking at their own PPE supply and they were concerned that they would have similar kind of issues. So that really drove, I think, the initial demand of the Badger Shield. The Badger Shield+ came out in around July. And when we had that intake form that I mentioned and showed you that plot of 22,000 units in just three days, 75% of those that requested Badger Shield+(s) were from schools. So they were essentially teachers for the most part. And the reason why is that right around that time was when people started realizing that schools are probably gonna reopen, at least they thought they would. And so there was that element of like wow, we really need to protect ourselves. You know, I saw this even personally. My sister’s an elementary teacher in Boulder, Colorado and she reached out to me around the same time.
And she was like, “I have to teach. What is the best PPE that I can get?” And so I think she represented what was going on across the world actually. And the final one, like I said, is very recent, so the full narrative hasn’t been really finalized yet, but it’s the Badger Seal. And we’ve really received a lot of interest from the general public. So we went from healthcare facilities to schools and now with the Badger Seal, it’s really the general public. In fact, the hospital hasn’t shown tons of interest in the Badger Seal so far. It’s mainly people just in the general public that want better protection when they’re going to the grocery store or maybe it’s at work. In the events going on right now, I think we all know, is that we’re kind of in the middle of this, what’s called the third surge, so there’s another surge in cases. With the colder temperatures in North America, people are moving more to the indoors, and I think now there’s more clarity on the impact of aerosols and so people want a better face mask. And so I think that’s likely why the Badger Seal has been popular.
So a few other reflections. Some of these I mentioned already. Is that it was pretty clear that the supply chains were extremely fragile during the crisis, and I think we all kind of learned that, and we saw it in first person. There was extreme power in distributed manufacturing. I told you that story of the factory in my hometown. Being able to manufacture things locally is extremely key during these times of crisis. I mentioned our role as a university. I think it’s kind of unique. A lot of people wondered if we would be making all these ourselves, and it was pretty clear to me that there was just no way we would be very good at making things in large quantities. It’s not really our core value, where we can add a lot of value.
But what I thought we did very well was identify needs, create open-source designs, be a hub for innovation with industrial and other partners, and do this supply chain support, these kind of bridges, those three bridges I mentioned. The other reflection and just reassurance and reaffirmation was really the strength of teams in general, but specifically interdisciplinary teams. It’s really not just engineers that can solve the problem. It’s engineers working with clinicians, it’s working with manufacturing partners, it’s working with policymakers. There are so many other stories I didn’t really go into, but it was an extremely expansive interdisciplinary effort that really required everyone to work together and collaborate. The other reflection was just the strength and the usefulness of rapid prototyping. We have a facility here that is all about rapid prototyping. All the prototypes that I showed you can see behind me here; it’s all about speed. So if you can generate 10, 15 prototypes in a few days, you can get that feedback and you can have a better design sooner. The next thing is just the pull must come from the users.
And I think that the projects that were of higher demand were the ones where the hospital actually reached out to us and said they needed something or some group reached out to us. If, like a perfect example is this compact PAPR, which Karl Williamson and I, who are the designers of this, love to pieces ’cause we designed it. But it really hasn’t gotten a lot of attention and the reason why is that we came up with it on our own and it wasn’t necessarily a pull. It was more of a push. So we knew that, and it was interesting to see that again. The next one is just designing for scalability. Kinda going back to that 3D printing model, in some ways you can 3D print for scalability, but what we did with most of our designs, we really thought about mass production and scaling up to the millions. The final thing was really the media. So it was interesting even with all those different spikes in interest that I mentioned with the Badger Shield, the Badger Shield+, and the Badger Seal. The other thing that definitely went hand in hand was where we had news articles.
We had information being shared in everything from more traditional to social media. Everything was helpful. One thing that surprised me is that I created a network essentially of collaborators in the media that were willing to share what we were doing. You know, the stories that they thought were relevant for their viewers. The local news was huge. Having local news come here on multiple occasions and highlight what we were doing, communicating what we were doing. They did an excellent job. I was extremely impressed with how well they were able to articulate the need and what we were doing from an engineering and manufacturing side. And also Facebook, Twitter, LinkedIn were all critical. Sharing that information on social media was essential in getting that information out and getting people familiar with what options they had.
So as I mentioned, really this is a story about people. We were all working together, focusing our talents and resources to help others. And it really just started out with this initial picture that I showed of Brian Ellison dropping off that 1,000 face shields. But I hope that you got the sense that it really grew to a lot more, and in the end there was a whole slew of projects that came out of it, and we’re still working on them and probably will until COVID is gone for good. But even beyond these projects, at the end, what we cared the most about was just the impact that we had on other people. So we want to make sure that we’re able to take the things that we’re doing here and share them with the world. In a lot of the same ways of what’s talked about with the Wisconsin Idea, I think that we represented some elements of that. There were so many people involved. I would like to thank all these people. There’s a quite a long list.
This is not a list of people that were kind of involved. These were people that were intimately involved with all of these projects. It required a huge number of people and it still does. So each of these people were involved in a very hands-on way. They were actively involved and they were critical to the success of all these projects. Well, I want to close by just thanking you for listening to this talk. If you’d like any more information, I encourage you to check out our website. We’ll have it linked below, and we have more information including videos and details on our open-source designs. So I wish you the best, and I hope you’re able to stay healthy during this time.
Search University Place Episodes
Related Stories from PBS Wisconsin's Blog

Donate to sign up. Activate and sign in to Passport. It's that easy to help PBS Wisconsin serve your community through media that educates, inspires, and entertains.
Make your membership gift today
Only for new users: Activate Passport using your code or email address
Already a member?
Look up my account
Need some help? Go to FAQ or visit PBS Passport Help
Need help accessing PBS Wisconsin anywhere?
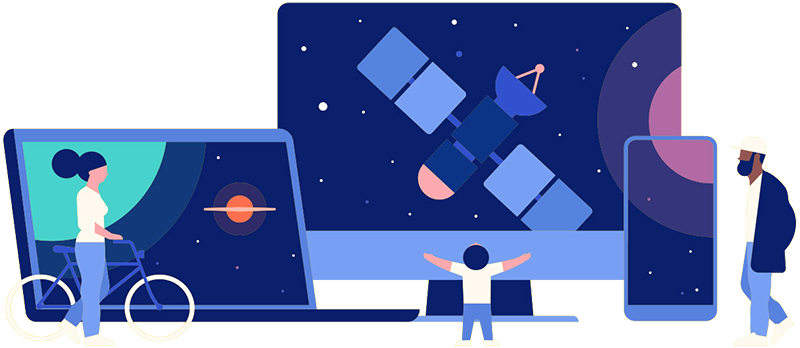
Online Access | Platform & Device Access | Cable or Satellite Access | Over-The-Air Access
Visit Access Guide
Need help accessing PBS Wisconsin anywhere?
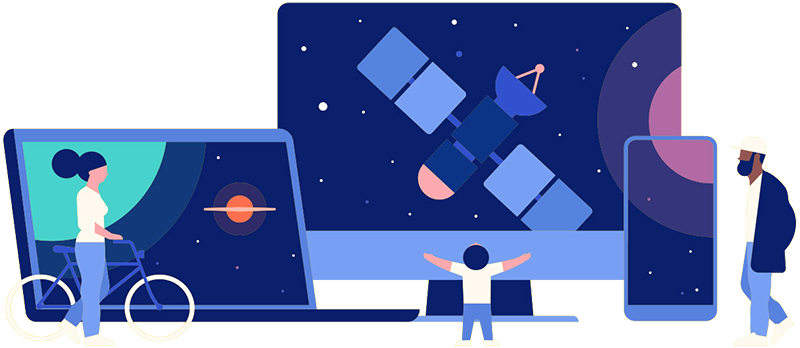
Visit Our
Live TV Access Guide
Online AccessPlatform & Device Access
Cable or Satellite Access
Over-The-Air Access
Visit Access Guide
Follow Us