Wisconsin Public Television
Transcript: In Wisconsin #905
Original Airdate: 4 November 2010
Patty Loew:
Welcome to “In Wisconsin.” I’m Patty Loew. This week, we take you to Sauk County, where nearly 70 years of Wisconsin military history are being ripped apart.
Man:
This cell was operating. It blew.
Patty Loew:
Plus a crop that can earn you $12,000 an acre.
Man:
For me being this size plantation it’s perfect.
Patty Loew:
We’ll show you how some farmers are returning to this cash crop of yesteryear.
Patty Loew:
Why would these Roxbury residents burn a piano with a turkey on top? We’ll explain next on “In Wisconsin.”
Announcer:
Major funding for “In Wisconsin” is provided by the people of Alliant Energy, who bring safe, reliable and environmentally friendly energy to keep homes, neighborhoods and life in Wisconsin running smoothly. Alliant Energy. We’re on for you. And Animal Dentistry and Oral Surgery Specialists of Milwaukee, Oshkosh and Minneapolis, a veterinary team working with pet owners and family veterinarians, providing care for oral disease and dental problems of small companion animals.
Patty Loew:
We begin this week with the end of an era. Piece by piece one of the US war machines built to stop the Nazis is being dismantled. The Badger Army Ammunition Plant is one of the last to go. Opening in 1942, it’s a massive military installation built on prairie between Sauk City and the Baraboo hills. Reporter Art Hackett first started reporting on demolition plans in 1998 and returned this past summer for a look at the evolution of the Badger Ammo plant.
Art Hackett:
The army decided it no longer needed the plant a dozen years ago. This is what it looked like in 1998. The landscape is dotted with nearly 1500 structures. This is the same perspective today. Only a few of the larger and more heavily contaminated buildings remain. Soon, they too will be gone.
Frank Anstett:
I think initially it’s very sad for myself and some of my coworkers that have been here a long time.
Art Hackett:
Frank Anstett began work with the plant mobilized during the Vietnam War.
Frank Anstett:
This was 24/7. You come over the hill at night, it was lit up in areas we were manufacturing rocket and single base and ballpark propellents. There was two rail lines serving us. We had two switch engines running 24/7.
Art Hackett:
His final duty is supervising the demolition of Badger.
Verlyn Mueller:
I grew up in this area, so I remember seeing the powder plant being built, seeing the earth-moving equipment out here and to a 4-year-old kid that was interesting.
Art Hackett:
Verlyn Mueller is with the Badger History Group, made up of former employees. They want the history to survive even though the buildings will not.
Verlyn Mueller:
You can’t tell the story of this powder plant without telling the story of the acquisition of the land, without acquiring the land, there was no powder plant. This was the Evangelical church. This is the Steadmans. A story to go with the Steadman farm. Mr. Steadman did not want to leave, so he had to be carried out of the house by his son. And when you acquire the land, you’re disrupting families, you’re disrupting people. And when you get right down to it, this is a story of human beings. It’s not a story of a place. It’s not a story of machines or buildings. It’s a story of the human beings who lived here and had to leave to make room for the powder plant and then it’s the story of the people who worked in those buildings to produce a product for war time use. At the peak, there were 13,000 people working out here. Considering the populations of Baraboo and Sauk Prairie at the time, no way were there 13,000 people in this area looking for work. Badger produced most of the propellant for three wars, World War II, Korea and Vietnam. Vietnam we produced almost all of the ball powder. Badger was the only government owned ball powder facility in the country.
Art Hackett:
In spite of the name, the Badger Ammo plant didn’t make ammunition. It made propellant.
Verlyn Mueller:
Ball powder looks like black grains of sand. It was a propellant that got the projectile from the gun to the target. The instruments in these panels I worked on. Every day you come in, there’s some things you don’t know where you’re going to go. You get called out to a problem somewhere, so I might be called out to nitroglycerin to replace a temperature gauge, or out in ball powder to work on an instrument on a ball powder still. Most of the time in a hazardous area.
Art Hackett:
Frank Anstett took us to one of the ball powder production buildings.
Frank Anstett:
I believe probably one of the primary reasons they reopened Badger was to provide propellant for small arms for Vietnam.
Art Hackett:
The highly explosive powder was hardened in these distillation tanks.
Frank Anstett:
This sill was actually operating. It was loaded and it blew.
Art Hackett:
At the time of the explosion Anstett was at work in another part of the plant.
Frank Anstett:
I remember feeling the ground shake, hearing the explosion and everybody looking at each other and everybody running out to look and see. You could see debris up in the air. The fire trucks, cause we had a full-time fire force at the time. Everybody headed in that direction. No one was hurt real bad, but there were guys right in the next still working.
Art Hackett:
In spite of the plant’s size and importance, Badger had an up and down existence.
Verlyn Mueller:
After World War II it was almost disposed of, then up again for Korea. Then down in the standby situation and then up again for Vietnam. Then after Vietnam ended in ’75, standby again.
Art Hackett:
Even though the plant was on standby, the army continued to invest money at Badger. Over the decades, Anstett says he helped move equipment from other newer powder plants which were being shut down. He helped install it at Badger, where it was an improvement over the World War II vintage gear. But he never got a chance to see it make powder.
Frank Anstett:
I think it was a difficult thing for us to accept because we spent most of all of our working career here maintaining it. It’s done now. Our mission now is to remove the plant and that’s what we’re doing.
Art Hackett:
One by one, the buildings are disappearing. The landscape is taking on the look of a city, leveled during one of the many wars Badger helped fight. In the place where the buildings once stood, it’s already returning to the prairie it was before Badger was built. It’s a new place, a place with a very long and unique history.
Patty Loew:
Demolition is expected to take another two years. When the plant is gone, prairie plants will take its place. Next week, “In Wisconsin” reporter Art Hackett gives you a closer look at what it takes to dismantle an ammunitions plant packed with explosives.
Man:
When they laid the place away, the standard was to clean it up to the point where there were no visible contaminants. That made it harder to find the explosives. I guarantee you they’re out there. We’re finding them every day.
Patty Loew:
The demolition of Badger Ammo next Thursday at 7:30 right here on Wisconsin Public Television’s “In Wisconsin.” Before World War I when the wave of German immigrants arrived in the 1800s, they brought with them a crop that would help Wisconsin emerge as a beer brewing capital. Today there’s a resurgence of microbreweries and a key ingredient for some brewers is the flour of the locally grown hops plant. Reporter Liz Koerner shows you how hops is making a comeback near Mazomanie.
Liz Koerner:
You can choose between Kiss the Lips or a Bitter Woman. How about Hopalicious or the mysterious Three Feet Deep? There are many more intriguing titles here, so many that beer coolers are bursting at the seams. Many of the offerings are created by craft brewers. In fact, there are now more than 300 craft brewers in the Midwest alone. Based on this bounty, one man set out to take advantage of the local brewing binge to benefit local farmers.
James Altwies:
Farmers in our area could really use a high-value crop that could be grown on small parcels of land.
Liz Koerner:
James Altwies is a horticulturist. Hes convinced that the flower of the hops plant will fit the bill.
James Altwies:
This variety is called Cascade. And what were looking for, this is a female flower. Okay? And do you see the yellow around the very tops of the petals here? Now we’re going to open it up. All that yellow is what we’re looking for. That is not pollen. Thats called lupulin. That’s where all the oils and the bittering power is for beer. This is the magic. That’s what we want right there.
Liz Koerner:
Hops is a crop that has a history here.
James Altwies:
20% of the hops produced came from Wisconsin in the 1860s.
Liz Koerner:
Back then, hops were in demand by the state’s German brewers, but insects and disease forced growers further west. Today hops varieties are more disease resistant, so Altwies created a business with friends and family called Gorst Valley Hops, offering information to growers, like this couple who are partners in the business.
Christine Molling:
When he brought up the subject of hops, I thought, that’s great. I have a hop plant growing on my deck. That’s easy. Well, growing one hop plant is pretty easy. Growing a whole acre of hop plants, that’s a little bit different.
Liz Koerner:
Hops require a lot of labor, starting with hand planting about 1,000 rhizomes per acre.
Christine Molling:
This is what all rhizomes look like when you get them. After the bed preparation is done, the planting part is pretty easy. As long as you have good knees.
Man:
We’ll do a lot more automated irritation.
Liz Koerner:
Gorst Valley Hops teaches its growers how to succeed with this unfamiliar plant. They also buy materials in bulk and pass on the discounts, a good thing since start-up costs for things like trellises and an irrigation system add up to around $10,000 an acre. Other benefits kick in after harvest.
James Altwies:
We do all the processing. We do all the chemical analysis. The USDA needs these things graded for physical qualities. We have to report those data. Then we also get them to the brewer. We make the sale.
Liz Koerner:
Matt Link from Black Earth planted an acre of hops a couple years ago. He says he relies on the support services offered Gorst Valley Hops.
Matt Link:
For me being this size plantation, it’s perfect.
Liz Koerner:
The biggest challenge for growers crops up at harvest time. The plants must be cut and moved to an area where the flowers can be picked off.
Matt Link:
These are about 15 feet off the ground. When they’re mature, it’s about 30 pounds per plant.
Liz Koerner:
It takes about a half hour to hand-pick each plant and the harvest must be done in a hurry.
James Altwies:
Each variety has about five days of peak ripeness. Not only is there a lot of work to do, it has to be done quickly.
Liz Koerner:
So far hops growers have been relying on friends and family to pick off the hops flowers because paying for pickers is cost prohibitive. But Tim Rehbein, an ag extension agent in Vernon County says growers can’t rely on free labor forever.
Man:
Less talking, more working. We’re done.
Man:
We have to go get more vines.
Man:
Yeah.
Tim Rehbein:
And it’s fun the first year. It may not be fun the second year. And the third year they don’t show up.
Liz Koerner:
So a mechanical harvester is a must.
Tim Rehbein:
Finding some method to assist in that cold pulling is going to be very beneficial.
Liz Koerner:
There’s one more hurdle that Gorst Valley must overcome. The price of hops changes every year based on availability. In 2010 their hops cost about four times more than hops from the Pacific Northwest, in part because Wisconsin growers don’t benefit from the economy of scale. It promises to be a hard sell to some, but one brewer is a return customer. Russ Klisch, the owner of Lakefront Brewery in Milwaukee, created a beer called Local Acre using hops from Gorst Valley and a Wisconsin-grown grain.
Russ Klisch:
It’s been great. Sold out the first year. It’s a nice, crisp lager. Its bold. We sell it in 22-ounce bottle. When you sell something in 22s, people expect a little extra, so we put extra hops and malt into that body and into that beer for everybody.
Liz Koerner:
He says there’s a market for local products, but quality has to come with it.
Russ Klisch:
Winemakers will talk about something called terroir, where you have a certain flavor that comes into a grape, can grow the same grape in France, California, Chile. All the same plants can have a different flavor to it. I do believe there is a flavor component that you get with a Wisconsin hops that’s very good.
Liz Koerner:
At the end of the third hops season, there is still a lot to learn and obstacles to overcome, but Altwies remains optimistic.
James Altwies:
Overall, I’d say that there’s no doubt that we can commercially grow hops in Wisconsin.
Patty Loew:
Gorst Valley is currently the only hops processing plant in Wisconsin. Its growers will have 50 acres of hops in production next year, including one in Michigan. When the plants are fully mature in three to four years, a grower can expect to net $7,000 to $12,000 a year. As a comparison, another labor intensive crop, grapes, can earn growers $4,000 an acre. Brewing beer is only one of the great Wisconsin traditions. There’s the smelt run in Sheboygan, Door County fishboil, and of course the summer solstice piano burning at the Roxbury Tavern. Never heard of it? Jo Garrett shows you how this tradition got started in Roxbury. And don’t forget the turkey.
Tom Grasser:
We have it on the Sunday closest to the solstice. We have a party out in the back where we have music and have beer and sandwiches. Then we celebrate the solstice by burning a piano.
Jo Garrett:
Tom Grasser, owner and operator of the Roxbury Tavern.
Tom Grasser:
We had a piano here a few years ago. It was going to cost a lot of money to have it hauled away. One of my employees, Rhonda, said why don’t we just burn it, have a piano burning and have a party and make up a story about it. We said that it was a Cajun tradition. When the Cajuns lived in eastern Canada, and they were in Canada, when a piano couldn’t be repaired anymore, they buried it in the family funeral plot. But when they moved to Louisiana that couldn’t be done anymore, because you dont bury anything in Louisiana, you burn it. So they burned the pianos.
Jo Garrett:
In truth, there is a tradition of piano burning. It comes from RAF pilots, England’s royal air force in World War II. There are many stories. One version has it that the pilots were deemed to be home once they crossed the so-called piano keys at the end of the runway. For those airmen who didn’t return, a glass of beer and mementoes were placed on the top of the piano and burned. Some wakes got out of hand and the entire piano went up in flames. So they say.
Jo Garrett:
West Side Andy, the band starts things off for young and old.
Tom Grasser:
We’ve had this party for, I don’t know, five or six or seven years, and no one’s called the police yet. And I figure maybe we’re not doing a good enough job.
Jo Garrett:
You can see the remains of past piano burnings in the vegetable garden that serves the restaurant portion of the Roxbury Tavern. So far, the solstice party had been problem-free when it comes to the local authorities. To ensure that happy state, Grasser has added a layer to the Roxbury piano burning that shows the kind of ingenuity that has made Wisconsin such a great party state.
Woman:
This is a raw turkey, so this is a legal cooking fire.
Tom Grasser:
So we cook a turkey inside the piano and then we eat it afterwards just to make it a cooking fire and I figure I won’t be able to get in much trouble that way.
Jo Garrett:
But on the way to soup, first the flambe. The fire marshal preps the piano. Maestro Larry Collins begins a medley of torch songs.
Tom Grasser:
It’s in our nature to come up with excuses to have a party. And to get together as a community, this community out there.
Jo Garrett:
This burning is a benefit.
Tom Grasser:
Today the money’s going to the Northwest Dane Senior Center. Those are the people that will be bringing my meals on wheels in a few years.
Woman:
Burn that thing!
Tom Grasser:
These are people who either work with the Northwest Dane Senior Center or they’re our customers or they live in the area or they heard about it and it’s community back there.
Jo Garrett:
Yes, a musical bonfire can build community, but must it be a piano that burns?
Tom Grasser:
People volunteer them. I could have had a dozen pianos out there. People want to get rid of them. Nobody wants them. They’re hard to haul.
Jo Garrett:
But why a piano? Why not bagpipes or an accordion?
Tom Grasser:
Yeah. Actually, that’s not a bad idea. One of my friends and customers is a musician and plays the banjo and of course banjo gets as many jokes thrown at them as accordions do. For example, what is perfect pitch? Well, that’s when you throw a banjo in the dumpster and it lands right in the middle without hitting the sides. Playing bagpipes while the piano burned would be a good idea because it’s a funeral. It’s sort of a dignified end to a life.
Jo Garrett:
It’s a celebration, of life and community, a chance to mark the turning of the seasons. Solstice, and the glory that is summer. Together.
Patty Loew:
Can’t wait for the piano burning at next year’s summer solstice? Well, there’s another event on the taverns calendar. To celebrate the spring equinox, it’s Socks on the Rocks as patrons throw their socks in a fire to say farewell to winter and welcome to spring. A new international exhibit remembering Milwaukee-born and University of Wisconsin-Madison alumna Mildred Harnack-Fish is on display, the only American woman executed on the order of Adolf Hitler. The exhibit With a Chosen Few, chronicles her life, love of translating and resistance work in Nazi Germany up until the day of her execution. German artist and professor Franz Rudolf Knubel shared his insights during a recent visit to Madison.
Franz Rudolf Knubel:
She was a very genuine Wisconsin woman. Everybody who met her was very imposed by her and attracted. What people said in the Third Reich, she was an important person in Berlin because she was married to a doctor. He worked in the ministry of economy, and he was a diplomat and was in charge with Soviet and US American diplomats. She at the one hand was helping him and the need for help was very intense. He was the head of this resistance group, the so-called Red Orchestra. The name of the title is a German word meaning a chosen few, In memoriam, Mildred Harnack-Fish. Her last poem she translated was I think Legacy is the translation, was the 16th of February, 1943, and this was the day of her execution. And she translated this poem and it is very moving. This is the place that the execution took place. It was just a very remote place in the prison. And to give testimony of this place, I think it’s something very evident, that you put a piece of paper on it and try to reproduce the traces with graphite. The prisoners were hanged or were guillotined. She must have stepped to this place or from this side to this place, because this was the guillotine, and this was the sink where her blood was going in when she was beheaded. It was walking through hell. If people realized what happened here and what is represented here, people begin to be silent because to know that at this place 3,000 people were executed, it’s not a normal situation. It is [ speaking in German ]. That means I loved Germany so much. And it said that these were her last words in her life. And this is very moving because she was condemned to death by this. I thought Mildred Harnack-Fishs destiny represents all the people who were killed under the dictatorship of the Nazis.
Patty Loew:
A powerful story. Some of that video was taken by Dustin Harnack, an architecture student in Berlin, a great-great nephew of Mildreds husband. This exhibit which first appeared in Berlin is making its US premiere at Hillel on the UW-Madison campus until December 3. Wisconsin Public Television is also in the process of producing a documentary about Mildred Harnack’s life in Milwaukee, Madison and in Berlin. To keep tabs on the documentary and other projects we’re working on, check out our blog, the Producer’s Journal. You can find the Producer’s Journal at wpt.org/inwisconsin for a look at upcoming reports. Finally this week, we take you to Harrington Beach state park. It has a mile of Lake Michigan shore, where you can enjoy the refreshing lake breeze while taking in Wisconsin’s Lake Michigan coastal landscape. Have a great week in Wisconsin.
Announcer:
Major funding for “In Wisconsin” is provided by the people of Alliant Energy, who bring safe, reliable and environmentally friendly energy to keep homes, neighborhoods and life in Wisconsin running smoothly. Alliant Energy. We’re on for you. And Animal Dentistry and Oral Surgery Specialists of Milwaukee, Oshkosh and Minneapolis, a veterinary team working with pet owners and family veterinarians, providing care for oral disease and dental problems of small companion animals.
Search Episodes

Donate to sign up. Activate and sign in to Passport. It's that easy to help PBS Wisconsin serve your community through media that educates, inspires, and entertains.
Make your membership gift today
Only for new users: Activate Passport using your code or email address
Already a member?
Look up my account
Need some help? Go to FAQ or visit PBS Passport Help
Need help accessing PBS Wisconsin anywhere?
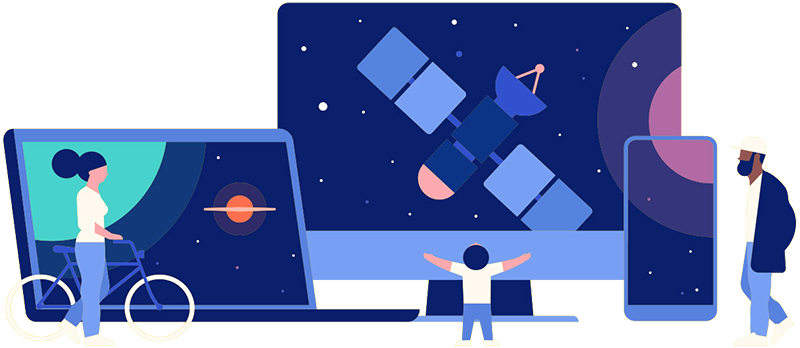
Online Access | Platform & Device Access | Cable or Satellite Access | Over-The-Air Access
Visit Access Guide
Need help accessing PBS Wisconsin anywhere?
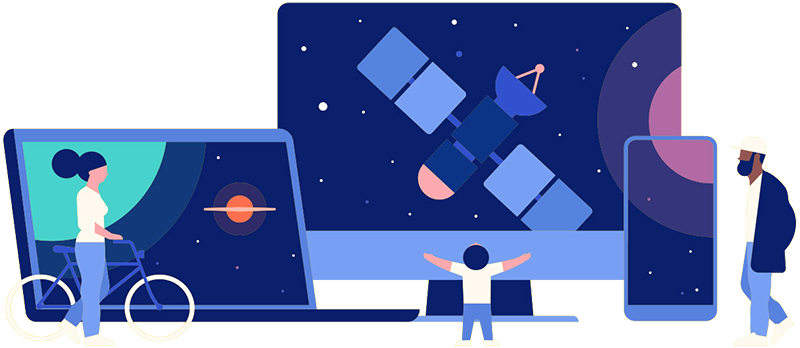
Visit Our
Live TV Access Guide
Online AccessPlatform & Device Access
Cable or Satellite Access
Over-The-Air Access
Visit Access Guide
Follow Us